Otkrijte mogućnosti unaprijeđenja održavanja primjenom CMMSa. Primjenom softvera Metrikon podignite održavanje opreme na višu razinu.
Glasovita 4.ta Industrijska revolucija je već naveliko prisutna među svim industrijskim segmentima. Pritisak na konkurentnost i efikasnost poslovanja nikada nije bio veći, a proizvodno orijentirane kompanije se moraju ubrzano prilagoditi zahtjevima tržišta žele li ostati na tržištu.
Jedan od načina kako unaprijediti poslovanje je uspostavom kvalitetnog sustava upravljanja opremom i strojevima, primjenom modernih tehnologija i digitalnih alata.
Održavanje imovine ima veliki potencijal za ostvariti uštede primjenom različitih računalnih sustava u kombinaciji sa strojnim učenjem, proaktivnim planiranjem radova i angažiranim sudjelovanjem svih uključenih djelatnika.
Računalni sustavi za upravljanje održavanje, skraćeno CMMS od engleskog Computerized Maintenance Management System vode poslovne procese i objedinjavaju sve potrebne podatke o održavanju.
Na primjeru softvera Metrikon za upravljanje održavanjem vidjet ćemo kako povećati efikasnost strojarskog održavanja te uhvatiti korak sa 4.tom industrijskom revolucijom.
Prilagodimo održavanje 4. Industrijskoj revoluciji
4. Industrijska revolucija nam je donijela spoj umjetne inteligencija (AI – artificial intelligence) i mehaničkih strojeva te zauvijek izmijenila način na koji strojevi prikupljaju i tumače podatke.
Proizvodni procesi premreženi su tako da omoguće strojno učenje i minimalan angažman ljudi, dok se podaci izmjenjuju u komunikaciji ljudi i robota u realnom vremenu.
Strojevi u proizvodnim pogonima bili su i ostat će uvijek podložni trošenju i imati potrebu za održavanjem.
Dosadašnje korektivno održavanje prakticira čekanje dok stroj stane ili se pokvari prije dijagnostičkog procesa otkrivanja koji dijelovi su potencijalno defektni i onda ih zamijeni.
Postavlja se pitanje: koliko je takva strategija održavanja dugoročno efikasna s obzirom na posljedice za okoliš, ljude, imovinu i profit?
Brojni strojni dijelovi su potrošni i imaju prirodnu tendenciju trošenju djelovanjem uzročnika iz okoline.
Zbog toga, intenzivnim praćenjem i bilježenjem moguće je predvidjeti koliko će ovi dijelovi trajati i uvesti fiksne intervale održavanja.Proizvodnja uvelike ovisi o isporučivanju proizvoda na vrijeme pa je glavni zahtjev da se strojevi što manje kvare, dakle da imamo što manje zastoja.

U isto vrijeme, povećane potrebe za održavanjem predstavljaju povećanje troškova, veći angažman resursa i više gubitaka u proizvodnji. Posljednjih godina cilj je uvesti strategije održavanja koje mogu unaprijed izračunati potrebe za održavanjem prije nego se dogodi kvar.
Održavanje temeljeno na motrenju stanja je jedna od takvih metoda, temelji se na mjerenju radnih parametara strojeva pomoću naprednih tehnologija, npr. inspekcija strojeva termo kamerom kako bi se utvrdilo ima li toplinskih gubitaka ili propuštanja radnog medija.
Računalni sustav upravljanja održavanjem ili CMMS je postao standardni alat za planiranje radova održavanja i praćenje troškova.
Jedan od takvih digitalnih alata je Metrikon. Ovaj računalni sustav za upravljanja održavanjem pruža robusnu funkcionalnost za upravljanje imovinom objekta, praćenje imovine i upravljanje radnim nalozima za pojednostavljenje performansi održavanja.

Računalni sustav Metrikon obuhvaća sljedeće funkcionalnosti:
- Imovina: objedinjava različite kategorije kao što su strojevi i oprema, sekcije postrojenja i prostori, a načini unosa podataka uključuju integraciju iz ERP sustava ili putem Excel tablica te prilaganje dokumentacije uz imovinu.

- Radni nalog: praćenje izvršenja radnog naloga u stvarnom vremenu, dodjela zadataka po radnom nalogu, obavijesti u stvarnom vremenu o aktivnim radnim nalozima, artiklima na skladištu i imovini koja se održava

- Metrike i indikatori: Ukupni troškovi radnih naloga, Troškovi rada na radnim nalozima, materijalni troškovi inventara, Ukupna količina i vrijednost potrošene, kupljene ili osnovne zalihe, Ukupan broj uspješnih/neuspješnih radnih naloga, Broj zastoja i vrijeme trajanja zastoja imovine,

- Inventar: povijest kretanja materijala i rezervnih dijelova, osiguranje minimalnih zaliha i kritičnih dijelova za ugradnju, mogućnost više skladišta, pregled ukupne i prosječne vrijednosti po artiklu, povijest unosa/utroška, dodavanje pratećih dokumenata poput videozapisa, slika, atesta i certifikata uz artikl

Primjenom CMMSa u poslovnim procesima održavanja podižete postojeću razinu učinkovitosti održavanja jer dobijete direktan uvid u radove održavanja kompanije i smjernice u kojim područjima imate prostora za optimizaciju aktivnosti održavanja.
Konfiguracija softvera se odvija brzo jer se radi o sustavu u oblaku kojem se pristupa putem interneta koristeći se računalom ili mobilnim uređajem sa bilo koje lokacije i u kojem god trenutku želite.
Podatke koji su važni za provođenje aktivnosti održavanja je moguće automatski uvesti u aplikaciju što isključuje potrebu da se oni ručno prenose kod inicijalne konfiguracije sustava.
CMMS je moguće integrirati sa postojećim informatičkim sustavima kompanije kao što je ERP.
Metrikon je razvijen na publish-subscribe tehnologiji koristeći MQTT protokol, čime podržava uspostavu IIoT infrastrukture za razmjenu podataka među različitim hardversko-softverskim sustavima.
Klasičan primjer rada u uvjetima IIoT infrastrukture bi bio primanje podataka o greškama u radu sa PLC-a proizvodne linije i na osnovu tih podataka automatsko kreiranje radnog naloga u Metrikonu.
Računalni sustav za upravljanje imovinom pruža mogućnost sveobuhvatnog planiranja, praćenja i optimizacije aktivnosti održavanja imovine, što će rezultirati poboljšanjem učinkovitosti, smanjenjem troškova i minimiziranjem zastoja u radu imovine.
Smanjenje troškova održavanja se postiže uštedom vremena u provođenju aktivnosti održavanja na način da se komunikacija među svim djelatnicima ubrzava, podaci potrebni za analizu stanja u održavanju se automatski prikupljaju i sve informacije o održavanju i servisna dokumentacija su dostupni na jednom mjestu.
Unaprjeđenje poslovanja korištenjem CMMSa se realizira kroz organizaciju preventivnog održavanja tako što se unaprijed definira koliki će biti troškovi materijala i rada te na osnovu toga će se vršiti korekcije za optimizaciju troškova.
Pored ovoga smanjenje troškova se može postići kvalitetnim upravljanjem skladištem rezervnih dijelova na način da ne dođe do nestanka rezervnog dijela kojeg bi trebalo biti na skladištu i da ne dođe do prekomjerne količine rezervnog dijela kojeg ne treba imati na skladištu u velikim količinama.
Prediktivno održavanje se temelji upravo na predviđanju kvarova analizom prikupljenih podataka i primjenom prediktivnih modela.
Upotreba novih tehnologija sada daje prednost motrenju stanja opreme jer kontinuirano prati stanje potrošnih dijelova kao što su remeni ili ležajevi.
Praćenje stanja je proces motrenja radnih parametara stroja (vibracije, temperatura, tlak…) kako bi se identificirale značajne promjene koje mogu biti protumačene kao znak početnog stadija kvara.
Ako kombiniramo motrenje stanja i CMMS, omogućavamo računalu primanje veće količine podataka za izradu točnijeg plana održavanja.
Jedan od novih koncepata koje uvodi 4. Industrijska revolucija je kibernetičko fizički sustav održavanja (Cyber Physical Maintenance Systems).
Ima istu namjenu kao i CMMS (planiranje radova održavanja), ali je istovremeno kibernetički spojen sa strojevima kako bi mogao prikupljati podatke pomoću senzora tijekom proizvodnje i osjetiti potrebu za održavanjem te planirati aktivnosti održavanja.
Unatoč opravdanim razlozima za uranjeno održavanje, često su radovi održavanja odgođeni ovisno o točnosti podataka koji odražavaju stanje dijelova proizvodnog stroja.
Uz brojna tehnološka unaprijeđenja, tvornica budućnosti će zahtijevati ažuriranje koncepta održavanja.
Velika količina prikupljenih podataka putem senzora bez prethodnog sortiranja ovisi o važnosti ili korisnosti.
Primjer je procesno postrojenje koje prikuplja podatke svake sekunde kako bi kontroliralo proizvodni proces i stvara oko 31.536.000 podataka iz samo jednog senzora tijekom cijele godine.
Promatranjem svakog podatka zasebno neće se stvoriti temelj za pokretanje aktivnosti održavanja, međutim analizom podataka mogu se utvrditi uzorci i trendovi koji se koriste u unaprijeđivanju radova održavanja, donošenju odluka ili kreiranju kapitalnih projekata.
Proizvodni sustavi već sada kontinuirano prikupljaju podatke od proizvodnih strojeva i povratnom vezom kontroliraju proizvodne procese.
Ovi podaci mogu biti korišteni u realnom vremenu i potom arhivirani. Rudarenjem podataka i primjenom analitičkih metoda za analizu može se pristupiti ovim podacima i koristiti ih za razvoj softvera za održavanje ili omogućiti kvalitetne povratne informacije djelatnicima u održavanju i proizvodnji.
Potencijal IoT (Internet of Things) i pristup većoj količini podataka iz sustava proizvodnje daju mogućnost za kvalitetno planiranje održavalačkih radova u kombinaciji s proizvodnjom bez škarta, čime se podiže konkurentnost i produktivnost.
Koje navike prakticiraju kompanije za efikasno održavanje strojarske opreme?
Svaka proizvodna kompanija, bez obzira na veličinu i proizvodne kapacitete, ima potrebu za održavanjem opreme i strojeva te za upravljanjem fizičkom imovinom.
Efikasno strojarsko održavanje doprinosi produktivnosti kompanije uz stalan trud da se odradi u zadanim rokovima, uz optimalno raspoređene resurse i uz što niže troškove.
Sada ćemo razmotriti koje navike u upravljanju održavanjem strojeva i opreme prakticiraju svjetske kompanije – lideri u strojarskom održavanju da bi ostale konkurentne i napredovale na tržištu.
Unaprijed moram upozoriti da niti jedna od navedenih navika nije apsolutna i 100% primjenjiva u svim industrijama, već služi kao skupina smjernica i ideja u kojim područjima imamo priliku poboljšati svakodnevno održavanje proizvodne opreme.
Krenimo redom:
Proaktivnost održavanja strojeva je prva navika koju praktciraju uspješne kompanije i podrazumijeva unaprijed definirati koje radove održavanja ćemo odrađivati i u kojem roku, obuhvaća planiranje resursa, materijala i rokova izvođenja radova.
Reaktivno održavanje poput vatrogasne postrojbe hitno reagira kada se određeni stroj pokvari, pogotovo ako je kritičan.
Suprotno tome, proaktivne tvrtke imaju uspostavljene programe preventivnog održavanja te planiraju radove temeljem kontinuiranog praćenja stanja opreme, čime se povećava pouzdanost strojeva a time i čitavog proizvodnog procesa.
Kada se dosljedno primjenjuju programi održavanja usmjerenog pouzdanosti tada kompanija upravlja stanjem opreme, za razliku od reaktivnog održavanja kod kojeg oprema diktira načine održavanja kompaniji.
Uspješne tvrtke su otkrile da se moraju pomaknuti na području smanjenja ili potpunog eliminiranja kvarova i to primjenom prediktivnog održavanja u kombinaciji s dosljednim planiranjem i raspoređivanjem radova.
Odjeli održavanja imaju planirane radove i dosljedno ih slijede.
Prema istraživanju europske federacije nacionalnih društva održavanja, 76% ispitanika smatra da njihove kompanije kontinuirano nastoje ulagati i unaprijeđivati održavanje, 19% ispitanika smatra sasvim suprotno dok 5% ispitanika nema mišljenje po pitanju stanja opreme i primjene naprednih tehnika održavanja.
Kompanije koje napreduju na ljestvici konkurentnosti zahvaljujući unaprjeđenju strojnog održavanja shvaćaju da se moraju mijenjati i proaktivno ulagati u razvoj održavanja kako bi napredovale i povećale profite na tržištu.
Određivanje ciljeva i redovita revizija postojećih ciljeva je druga navika koju prakticiraju kompanije uspješne na području strojarskog održavanja.
Efikasna kompanija ima razvijene strateške planove za različite odjele u koje su uključeni svi djelatnici.
Planovi postoje u digitalnom obliku i dostupni su svima.
Planovi se odnose na strategiju održavanja — koji pristup održavanju je prioritetan?
Koji radovi se unaprijed planiraju i raspoređuju?
Tko i temeljem kojih kriterija određuje koji strojevi će se popraviti prvi?
Provjerava se strategija pouzdanosti – primjenjujete li prediktivne tehnike održavanja na svu opremu koju imate ugrađenu u postrojenjima ili samo na određene strojne sustave?
Hoćete li koristit praćenje stanja u realnom vremenu ili praćenje na bazi tjednih ruta obilaska opreme?
Koristite li rezultate analize podataka preventivnog održavanja za unaprijediti postojeću situaciju?
Imate li obučene djelatnike za razvoj i primjenu metodologija održavanja usmjerenog pouzdanosti?
Strategija upravljanja materijalom – imate li skladište ispunjeno rezervnim dijelovima prema potrebama ili je skladište stalno prepunjeno bez obzira na stvarne potrebe?
Na kojim kriterijima se temelje odluke o količini materijala na skladištu?
Imate li definirane liste rezervnih dijelova u računalnom sustavu upravljanja održavanjem CMMS? Tko unosi i prati podatke?
Strategija obuke zaposlenika – imate li definirane planove stručnog razvoja zaposlenika zaduženih za održavanje strojeva?
Imate li dovoljan broj specijaliziranih djelatnika, podizvoditelja, alata i uređaja za provođenje definiranih strategija održavanja?
Odgovori na ovakva i slična pitanja ukazuju na stanje održavanja u kompaniji tako što identificiraju uspješna područja i ne tako uspješna područja gdje je potrebno poraditi ubuduće i unaprijediti razvoj kompanije. Uz ovu strategiju povezuje se navika kontinuiranog unaprjeđivanja kompetencija djelatnika.
Efikasne kompanije su prepoznale potrebu za ulaganjem u znanja i vještine djelatnika kako bi ostale konkurentne i napredovale na tržištu.
Kada kompanije proaktivno educiraju i treniraju djelatnike, trebaju to raditi ovisno o krajnjem cilju koji žele postići, npr. edukacija iz održavanja prema pouzdanosti nema puno smisla ako djelatnici još nisu savladali osnove preventivnog održavanja.
Prvo se određuje koju razinu znanja i vještina djelatnici posjeduju u ovisnosti o strategiji razvoja kompanije, protom se određuje koje edukacije i treninzi su potrebni, kojem broju djelatnika i koje razine kompleksnosti.
Razvoj novih vještina je dvostruko koristan, u prvom redu djelatnicima raste razina kompetencija i drugo, kompanija ima koristi jer zapošljava educirane djelatnike koji doprinose njenoj konkurentnosti.
Kompanije koje nemaju jasno definirane ciljeve i posvećenost njihovom ostvarenju usvajaju alate i metode za povećanje pouzdanosti stihijski i bez prethodnog planiranja i kasnije analize, bez da iskoriste sve prednosti kvalitetnog programa pouzdanosti.
Stihijska implementacija bilo kakvog program održavanja bez osnovnog razumijevanja i analize je dugoročno uzaludan posao.
Imajući krajnje željene ciljeve na umu, posvećenost razvoju efikasne tvrtke, korištenje svih pogodnosti CMMS-a, planiranje i raspoređivanje radova održavanja unaprijed te redovito provođenje analiza o uzrocima i posljedicama kvarova dugoročno donose rezultate i vraćaju uloženo u obliku pouzdanog rada postrojenja, minimalnog broja kvarova i neplaniranih zastoja te većih profita.
Paradoksalno, glavni cilj učinkovitog održavanja trebao bi biti što manje aktivnosti održavanja uz predvidljivu svakodnevicu.
Usmjerenost prema ciljevima temeljem preventivnih planova održavanja je navika profesionalnog upravljanja.
Potrebno je organizirati i rasporediti radove tako da su u skladu s prethodno definiranim ciljevima.
Ako su ciljevi na prvom mjestu (ili mentalna vizija što želimo postići održavanjem) onda se ciljevi u fizičkom svijetu manifestiraju kroz organizirani plan primjene.
Dokumentirani planovi održavanja omogućavaju pravodobno određivanje redoslijeda radova ovisno o prioritetima.
Koraci u uspješnoj primjeni planova održavanja se određuju ovisno o procjeni postojećih praksi održavanja i postojećoj razini pouzdanosti opreme (ili njenom nedostatku).
Obično se najbolji rezultati dobiju kada nakon određenog vremena napravite neovisnu analizu i procjenu.
Koraci za poboljšanje koje dobijte kao rezultat uključuju, ali nisu isključivo ograničeni na područja:
- poslovnih procesa (uspostava organizacijske kulture usmjerene na pouzdanost, razvoj ključnih pokazatelja uspješnosti KPI, razvoj toka aktivnosti za sve važne radove),
- osnovnih strojarskih elemenata (uspostavu listi rezervnih dijelova, prioriteti opreme prema kritičnosti),
- strategiju upravljanja zalihama (standardizaciju sadržaja rezervnih dijelova u skladištu, razvoj listi rezervnih dijelova, integraciju skladišnog poslovanja u poslove procese, optimizaciju raspoloživih zaliha),
- pouzdanost (određivanje osnovnih zahtjeva za prediktivnim održavanjem, redovite analize FMEA, analize uzroka i posljedica kvarova RCMA, primjenu odgovarajućih metoda prediktivnog održavanja, razvoj i optimizaciju preventivnog održavanja),
- obuku djelatnika (procjenu postojećih vještina, razvoj novih vještina održavanja, plan obuke prema potrebama).
Svaki korak u planu treba pratiti, mjeriti rezultate, prilagođavati po potrebi i pridržavati se redoslijeda.
Kada se dogodi istovremeni kvar dvaju jednako važnih strojeva, djelatnici trebaju započeti s popravkom prema kritičnosti stroja za rad proizvodnog procesa i prema prioritetu.
Radi pojednostavljenja, preporučuje se koristiti matricu prioriteta Hitno/Bitno, tkz. Eisenhowerovu matricu.
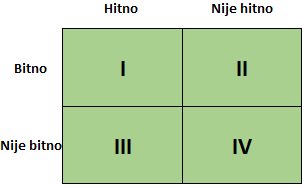
U I kvadrantu se nalaze kompanije koje većinu vremena odrađuju reaktivno održavanje, pri čemu je otklanjanje svakog novog prijavljenog kvara hitno i bitno.
Nitko ne vrši određivanje prioriteta, nema kritičkog pristupa održavanju i sve mora biti čim prije odrađeno.
Ovakav pristup ne samo da je stresan i iscrpljujući, već dugoročno ne donosi nikakve rezultate i u potpunosti se gube iz vida bilo kakvi ciljevi i planiranje kojim bi se povećala pouzdanost rada i konkurentnost kompanije.
Drugim riječima, put do pakla popločen je jurnjavom za hitnim otklanjanjem kvarova.
U II kvadrantu se nalaze bitne aktivnosti koje ne zahtijevaju hitnu reakciju, poput pregleda opreme, primjene prediktivnog održavanja, otvaranja radnih naloga za predstojeće radove te unos podataka u CMMS.
Dugoročni cilj bi treba biti prijelaz iz I u II kvadrant i proaktivna usmjerenost na planirane radove koji su u konačnici jeftiniji od reaktivnih popravaka.
Što se više zadržavamo u II kvadrantu, to ćemo postići bolje rezultate u strojnom održavanju.
U III kvadrantu su nebitni radovi koji dobiju prioritet hitnih, većinom iz nesigurnosti uključenih sudionika i nedovoljnog poznavanja stanja opreme ili proizvodnog procesa.
Radovi donose kratkotrajnu korist ili mentalnu sigurnost ali na štetu planiranih radova i rušenja čitave koncepcije učinkovitog raspoređivanja resursa uz narušavanje međuljudskih odnosa, zbrku u svakodnevnom radu i prebacivanje/izbjegavanje odgovornosti.
U IV kvadrantu su nebitni radovi koji nemaju hitan prioritet. Svjesni smo da se takvi radovi moraju odraditi u nekom periodu tijekom godine, ali nema pritiska niti strogo definiranih rokova npr. godišnje uređivanje raslinja uz prometnice, sanacija manjih pukotina u asfaltu, zamjena oštećene ograde uz granice postrojenja i sl.
Uspješne kompanije u traženju rješenja za probleme održavanja polaze od pitanja kako će neka aktivnost utjecati na postojeće procese?
Ako će poboljšati jedan proces a nanijeti štetu drugim procesima, dugoročno znači da predložena aktivnost ne donosi korist.
Sva rješenja moraju poboljšati situaciju svih sudionika uključenih u proces je smo svi dio istog procesa/kompanije.
Stalna i konkretna komunikacija pomaže u raspoređivanju radnih planova održavanja unutar razumnog vremenskog okvira i dozvoljava efikasno korištenje resursa.
Također, komunikacija je u aktivnom slušanju djelatnika održavanja, operatera proizvodnog procesa i izvođača radova – ustanovite o čemu se zaista radi prije nego krenete u akciju kako biste razvili pozitivne odnose među ljudima.
Što znači kada netko kaže Ne?
Što znači kada netko inzistira da se stroj snage preko 100 kW mora vratiti s popravka za 12 sati? Je li razumljivo objašnjeno kako kvalitetni popravci kompleksnih kvarova traju dulje vrijeme, pogotovo kada je u pitanju reaktivno održavanje jer je stroj doživio neplaniranu havariju?
Dok zaista nismo svjesni zašto su zabrinuti uključeni sudionici, nismo u mogućnosti naći rješenje koje će biti obostrano korisno.
Efikasne kompanije se pobrinu da svi sudionici iznesu svoje brige o potencijalnim posljedicama prije nego krenu poduzimati određene korake.
Sinergija je navika stalne međusobne suradnje, podsjeća nas da je cjelina veća od zbroja pojedinačnih dijelova, što znači da trebamo tražiti i uključiti zajednički doprinos.
Kako bismo dobili pobjedničko rješenje za sve uključene strane, potrebno je proaktivno sudjelovati i ustanoviti što je zaista potrebno postići održavanjem strojeva u proizvodnom procesu.
Možda popravak nekog stroja dulje traje jer je potrebno izraditi nove dijelove koji trenutno nisu raspoloživi na skladištu i čija isporuka traje nekoliko mjeseci, a stroj mora biti u funkciji unutar 24 sata ili nije bilo raspoloživih zavarivača koji bi pokrpali oštećeno spiralno kućište i sl.
Na ovakav način jasno se i jednoznačno prenose informacije o postojećim problemima, načinima njihova otklanjanja i uloženom trudu u traženje rješenja.
Zajedničke aktivnosti kojima se ostvaruje sinergija su održavanje usmjereno pouzdanosti, analiza uzroka i posljedica kvarova (RCFA), rangiranje opreme prema kritičnosti za proizvodni proces te analiza povratnih informacija o prethodno planiranim radnim nalozima i po njima odrađenim radovima.
Da rezimiramo, navike kompanija koje provode efikasno strojarsko održavanje su zajedničko djelovanje, stalna komunikacija, suradnja, određivanje ciljeva i usmjereno djelovanje prema postizanju tih ciljeva te neprekidna proaktivnost.
Tekst je nastao temeljem prezentacije tvrtke Neuros.
Koje navike u održavanju prakticira vaša kompanija? Kakve rezultate postiže? Koje navike planirate usvojiti ubuduće? Jeste li već prilagodili vaš sustav održavanja 4.Industrijskoj revoluciji? Podijelite svoja iskustva sa mnom u komentarima!