Priručnik za Upravljanje održavanjem i inženjering (Handbook of Maintenance Management and Engineering) napisala je skupina autora (Jezdimir Knežević ,Mohamed Ben-Daya, Salih O. Duffuaa, Abdul Raouf, Daoud Ait-Kadi), svi redom sveučilišni profesori s različitih fakulteta.
Službeni opis priručnika s web stranice nakladnika kaže sljedeće:
Priručnik Upravljanje održavanjem i inženjering pokriva širok izbor tema iz održavanja na teorijskim temeljima, znanstvenim istraživanjima te najavljuje nadolazeće trendove u znanstvenom području strojnog održavanja.
Jedno od glavnih poslovnih područja svake proizvodne kompanije bez obzira na branšu, veličinu i broj djelatnik je interdisciplinarnost strojnog održavanja; priručnik daje iscrpne analize, kvantitativne i kvantitativne preporuke za procjenu sustava održavanja te fundamentalna i primjenjiva istraživanja iz šireg spektra održavanja, predlaže rješenja određenih situacija i upućuje na vještine upravljanja potrebne za evaluaciju i kontinuirano unaprjeđenje sustava održavanja.
Da bi bile konkurentne na domaćim i inozemnim tržištima, proizvodne kompanije moraju funkcionirati uz visoku razinu pouzdanosti strojeva i opreme kakva je bila nezamisliva i teško dostižna proteklih desetljeća. Zahtjevi za kvalitetom proizvoda, sve kraćim vremenom zastoja proizvodnog procesa i povećanom operativnom efikasnošću unutar brzo promjenjive okoline zahtijevaju visoku razinu održavanja.
U nekim slučajevima pred održavanje se postavlja zahtjev povećanja proizvodne učinkovitosti i profita te zadovoljstva krajnjih kupaca, uz istovremeno snižavanje kapitalnih i operativnih troškova.
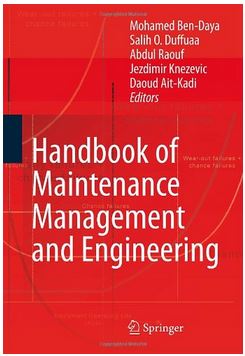
S obzirom na navedene izazove, strategija održavanja mora biti skladu sa zahtjevima proizvodnih procesa i postojećom dobrom praksom.
Teme su izabrane tako da pokrivaju širok raspon problematike iz upravljanja održavanjem i inženjeringa kako bi pomogle svim zainteresiranim za održavanje bilo da su industrijski praktičari ili akademski istraživači.
Održavanje je u svim industrijama postalo multidisciplinarno područje i susrećemo se sa situacijama gdje je održavanje u potpunosti odgovornost djelatnika koji ne moraju nužno imati inženjersko obrazovanje.
Priručnik zato ima cilj pomoći djelatnicima na različitim razinama da bolje razumiju i savladaju izazove strojnog održavanja, bilo da se radi o voditeljima pogona, inženjerima, djelatnicima proizvodnje, iskusnim održavateljima ili početnicima u održavanju.
Priručnik je istovremeno kvalitetan resurs za tehničare, inženjere i sve djelatnike koji su na bilo koji način uključeni u održavanje strojeva i opreme.”
Što se tiče izvedbe, priručnik je podijeljen u 6 područja i sadrži 26 poglavlja na 700-tinjak koja pokrivaju širok raspon tema iz upravljanja održavanjem i inženjeringa.
Priručnik daje enciklopedijski pregled područja poput održavanja usmjerenog na pouzdanost, integrirano e-održavanje i inteligentni sustavi održavanja, utjecaj održavanja na okoliš, ljudske pogreške i siguran rad postrojenja, analize kvarova i stabla odlučivanja, razvoj računalnog sustava za upravljanje održavanjem, matematičko modeliranje na razini komponente, stroja i strojnog sustava…
Za razliku od priručnika koje sam do sada proučavala i koristila te napravila recenzije u člancima Održavanje i popravak strojnih elemenata, Održavanje usmjereno na pouzdanost, Potpuni vodič za preventivno i prediktivno održavanje, Inženjerski vodič za rotacionu opremu, ovaj priručnik je totalno drugačiji prvenstveno što se tiče pristupa i obradi teme te razini kompleksnosti.
Vidljiva je velika razlika u načinu pisanja koji je više orijentiran teorijski i stavu prema strojarskom održavanju iz pozicije profesora sa sveučilišta u usporedbi s priručnicima koje su napisali profesionalci s višegodišnjim praktičnim iskustvom u svakodnevnom radu na strojevima.
Opisani i razrađeni praktični primjeri su starijeg datuma te se većinom odnose na avionsku industriju, vojnu industriju, rudarstvo, automobilsku industriju i željeznice, vjerojatno zato što su autori svoj akademski rad usmjerili na ta područja.
Poglavlja usmjerena na upravljanje održavanjem predstavljaju strukturu organizacije kakva bi trebala biti da se izvuče maksimalna učinkovitost iz radnog procesa, djelatnika i resursa.
Priručnik je pretežito namijenjen održavanju u velikim kompanijama koje imaju više sličnih ili različitih procesnih postrojenja unutar iste grupacije.
Iznesene principe i preporuke morate staviti u perspektivu održavanja kojim se bavite, npr. ako radite održavanje farmaceutskog proizvodnog pogona prilagodit ćete principe takvoj vrsti postrojenja, za razliku od kolega koji rade u petrokemiji i koji će napraviti drugačiju prilagodbu radi specifičnosti strojeva o kojima brinu.
Poglavlja usmjerena na inženjering bave se unaprijeđenjem postojećih održavateljskih sustava i razradom optimizacije procesa.
Izneseni su brojni matematički modeli za izvođenje različitih vrsta analiza kojima ćete detaljno modelirati prošlo i buduće stanje strojeva i strojnih sustava. Analize se sastoje od najjednostavnijih koncepata do složenih matematičkih formula, što je razumljivo kada uzmemo u obzir da različite industrije imaju različiti stupanj razvoja u održavanju.
Poglavlja su isključivo računski orijentirana ako trebate napraviti detaljnije analize ili kao pomoć pri izračunavanju parametara koji su od koristi za provjeru pouzdanosti rada vaših strojeva.
Naći ćete kvalitetne primjere na koji način korak po korak napraviti analize pouzdanosti pojedinačnih strojeva i čitavih skupina na postrojenju, analize pojedinačnih komponenti i svih komponenti u promatranom stroju, razvoj stupnja trošenja te razvoj kvara tijekom vremena.
Priručnik će dobro poslužiti ako vam je poslovni plan napraviti optimizaciju rada postojećih strojeva temeljem matematičkih modela i analiza jer ćete dobiti konkretne brojke o tome kolika je projekcija učestalosti kvarova za sustave sa različitim brojem komponenti.
Prema mojem iskustvu korisna poglavlja su bila: sustav upravljanja održavanjem, izrada i poboljšanje svakodnevnih radnh naloga, kvaliteta izvršenog posla, implementacija sustava održavanja usmjerenom na pouzdanost, određivanje prioriteta u popravcima te ciljevi koje mora ispuniti svaki popravak bez obizra na kompleksnost stroja.
Korisno za praktičnu primjenu su još načini kako izračunati pokazatelje uspješnosti održavanja, modelirati ponašanje stroja u budućnosti temeljem poznatog broja kvarova i primjenjenih održavateljskih tehnika te procjenu učinkovitosti održavanja po pitanjima:
Koji održavateljski poslovi moraju biti odrađeni?
Kada održavateljski poslovi moraju biti odrađeni?
Koliko je kompleksno izvršiti određeni održavateljski posao?
Je li sigurno izvršiti određeni održavateljski posao?
Koliko je djelatnika potrebno za izvršiti određeni održavateljski posao?
Koliki je trošak popravka?
Koliko dugo će strojni sustav biti u kvaru?
Koji alati i uređaji su porebni za popravak? i
Koji stručni djelatnici trebaju za popraviti stroj?
Priručnik također upućuje na korelacije između performansi opreme i broja intervencija koje se rade u analizama pouzdanosti radi određivanja koliko je vremena proteklo od pojave prvog kvara ili koliko je prošlo vremena između 2 kvara i sve to u odnosu na količinu proizvoda određenog postrojenja te utjecaj održavanja na sigurnost.
Učinkovitost se promatra kroz održavanje po radnim satima pojedinih stručnih djelatnika ovisno o radim satima sustava, ciklusima rada sustava održavanja po mjesecima i po održavateljskom poslu uz praćenje troškova.
Zanimljivo je i poglavlje o načinima kako izračunati i izraditi projekciju održivosti strojnog sustava kada je najveći utjecaj na dugovječnost u fazi konstruiranja stroja pa možete vidjeti koje su razlike u životnom vijeku u odnosu na tehničke karakteristike za različite varijacije konstrukcije.
Vrlo rijetko se u strojarskoj literaturi razmatra utjecaj garancije na održavanje jer budimo realni, koliko puta i kada smo i sami u praksi analizirali utjecaj garancije?
Često je odgovor – samoinicijativno nismo nikada, osim u slučaju kada stroj doživi žešću havariju tijekom trajanja garancije pa slijedi popravak i dugotrajno druženje sa ovlaštenim servisom ili predstavnikom proizvođača 😉
Priručnik nam također može pomoći pri uvođenju RCM-a jer ukazuje na dokument SAE JA-1011 američkog Society of Automotive Engineers koji daje određeni stupanj standardizacije za procese održavanje usmjerenog prema pouzdanosti te defnira proces kroz 7 pitanja temeljem kojih kasnije određujete pristup održavanju.
Pitanja glase:
- Koja je funkcija i povezani standardi performansi opreme i strojeva u sadašnjem radnom okruženju?
- Na koje načine stroj ne može ispuniti svoje funkcije?
- Što uzrokuje svaki kvar ili nemogućnost ispunjavanja funkcije za koju je stroj namijenjen?
- Što se dogodi sa strojem i sustavom kada se desi svaki kvar?
- Na koje načine je bitan svaki kvar (utjecaj na zdravlje, sigurnost, okoliš)?
- Što se može učiniti da se predvidi ili spriječi svaki kvar?
- Što treba učiniti ako nema primjenjivi proaktivnih rješenja za ublažavanje kvara ili potpuno spriječavanje?
Navedena pitanja vam mogu puno pomoći ako ste i sami u procesu uvođenja održavanja usmjerenog prema pouzdanosti ili vas podsjetiti da ih iskoristite za analizu i poboljšanje sustava održavanja koji već imate.
Dodatno, ukupnu produktivnost održavanje dijela proizvodnog postrojenja ili čitavih pogona možete procijeniti analizom koja obuhvaća sljedeće:
- Izbor sustava i prikupljanje potrebnih podataka
- Definiranje granica sustava
- Opis sustava i izradu funkcionalnih blok dijagrama;
- Provjeru funkcionalnosti sustavaa i učestalost kvarova
- Načine nastanka kvarova i analiza utjecaja (Failure mode and effective analysis – FMEA);
- Izradu logičkog stabla odlučivanja te
- Izbor zadataka koji će se implamentirati radi poboljšanja postojećeg stanja.
Priznajem da imam podvojeno mišjenje o ovom priručniku zato što je s jedne strane previše teorijski a mi smo ipak praktičari, dok s druge strane ima dosta razrađene matematičke modele koje možete preuzeti za obradu vaših podataka i direktno unositi formule u excel ili u kojem god programu radite analize pa štedite vrijeme i energiju.
Za kraj donosim popis prednosti i nedostataka pa vi sami prosudite kolika bi vam bila korist od ovakve vrste priručnika.
Prednosti Priručnika za Upravljanje održavanjem i inženjering:
Sviđa mi se što su navedene naučene lekcije iz područja upravljanja održavanjem kao smjernica inženjerima za buduće: konstruiranje, sklapanje sustava, projektiranje i instalaciju električnih kabela, elektronskih sklopova, ispitivanja opreme, brtvljenja i podmazivanja.
Objedinjene su brojne smjernice i korisna pitanja koja vas vode pri procjeni stanja vaših strojeva i opreme, tj. sve što sam navela u prethodnim paragrafima i još više.
Na jednom mjestu imate brojne matematičke modele koji idu korak po korak pod uvjetom da ste prethodno prikupili sve podatke.
Nedostaci priručnika:
Autori za svako poglavlje daju reference na postojeću literaturu i (uglavnom vlastite) članke iz određenog područja, ali reference su stare 10 i više godina.
Stil pisanja je u potpunosti akademski te autori često citiraju svoje prethodno objavljene znanstvene radove. Za izradu analiza potreban je veliki broj uzoraka ili komada opreme pa je bolje koristiti matematičke modele za analizu stanja u velikim postrojenjima sa brojnim strojevima istog tipa npr. ako imate 50 pumpi, 30 parnih turbina male snage, 20 ventilatora i sl.
Potrebno je puno truda i vremena za empirijsko prikupljanje podataka i parametarski pristup modeliranju pod uvjetom da imate kvalitetne i istinite podatke koje ste sami provjerili.
Nema smjernica za provjeru kvalitete prikupljenih podataka, matematički modeli zahtijevaju napredno poznavanje matematike i statistike, pogotovo za tumačenja rezultata.
Definicije iz održavanja i podjele se ponavljaju iz poglavlja u poglavlje što pomalo postaje monotono, valjda su se autori vodili izrekom – ponavljanje je majka mudrosti.
Iako je priručnik između ostalog namijenjen i početnicima u održavanju, mislim da će početnicima biti teže razumljiv i morat će uložiti više truda i vremena u proučavanje (da ne spominjem pokušaj primjene u praksi) jer izneseni principi ipak zahtijeva određeno prethodno iskustvo za praćenje i razumijevanje sadržaja .
Koji stručni priručnik koristite u praksi? Zašto? Podijelite vaša iskustva u komentarima ili mi napišite recenziju i na taj način podijelite kvalitetnu literaturu s kolegama pa ću objaviti vašu recenziju na blogu!