Pumpni agregati za svoj rad troše 20%-25% energije u procesnom postrojenju. Iako se kupuju zasebno, svaki pumpni agregat (sastavljen od pumpe, elektromotora i spojke) funkcionira samo unutar procesnog sustava. Količina energije i radnog medija ovise o konstrukciji pumpe, konstrukciji strojnog sustava i načina na koji se odvija proizvodni proces. Ovi čimbenici su neovisni i moraju si međusobno odgovarati tijekom čitavog životnog vijeka da bismo ostvarili minimalnu potrošnju energije i minimalne troškove održavanja, dug radni vijek i maksimalnu iskoristivost.
Početni trošak kupovine opreme je samo mali dio ukupnog troška životnog vijeka za pumpe velike iskoristivosti. Danas ćemo razmotriti koji sve čimbenici utječu na ukupan trošak životnog vijeka pumpnog agregata kako bismo bolje razumjeli funkcioniranje dijelova i identificirali situacije za smanjenje potrošnje energije, rada i održavanja. Životni vijek prosječno pumpnog agregata je 20 do 25 godina, iako u Hrvatskoj postoje proizvodna postrojenja s pumpama starijim od 30 godina.
Na slici 1. imamo primjer jednostavnog pumpnog agregata (lijevo) te grubu raspodjelu troškova tijekom njegovog životnog vijeka (desno) koje čine troškovi održavanja, troškovi energenata, troškovi nabave i ugradnje te objedinjeno čitav niz manjih troškova.

Slika 1. Pumpni agregat i raspodjela troškova
Metode za analizu životnog vijeka postojećih pumpnih agregata
Prije nego što započnemo čitav proces kalkulacije troškova životnog vijeka za novi pumpni agregat, preporuča se provjeriti trošak životnog vijeka postojećih pumpnih agregata koje već imamo ugrađene na proizvodnim postrojenjima poput ovog na slici 1. Prednost je što za postojeće agregate već imamo određenu količinu povijesnih podataka o kvarovima, troškovima nabave, popravaka, održavanja i sl. Za početak treba prikupiti sve dostupne podatke o pumpnim agregatima, odrediti potrebne protoke za sustav prepumpavanja, provjeriti jesu li gubici u sustavu svedeni na najmanju moguću mjeru te odrediti koji agregati imaju najveće troškove održavanja.
Prilikom analize možemo koristiti 2 metode:
1) promatranje rada stvarnog sustava: bilježe se promjene tlakova, diferencijalnih tlakova i protoka radnog medija u sustavu cjevovoda i analizom prikupljenih podataka u realnom vremenu. Ova metoda omogućava pregled rada stvarnog sustava, međutim fizikalna ograničenja proizvodnog procesa i prisutni rizici onemogućavaju eksperimentiranje s većim varijacijama radnih parametara. Drugim riječima, ako u određenom momentu pretjerate s povećanjem protoka, možete izbaciti pumpu iz rada i time obustaviti proizvodni proces a takvu vrstu eksperimentiranja vam u stvarnosti neće dozvoliti niti jedan voditelj postrojenja
2) izračun primjenom tehnika mehanike fluida, stvaranjem matematičkog modela za sustav cjevovoda i potom računanja tlaka i protoka u određenim točkama cjevovoda. Matematički modeli omogućavaju brojne varijacije i istraživanje alternativa, međutim imajte na um da niti jedan model nije 100% savršen i da ga svakako treba provjeriti u stvarnim uvjetima rada.
Bez obzira na vrstu provedene analize, vaš krajnji cilj će biti dobivanje cjelovite slike o tome kako funkcioniraju pojedini dijelovi strojnog sustava u kojem radi pumpni agregat, utjecajima procesnih parametara na njegov životni vijek te određivanju potencijalnih karakteristika koje je moguće optimizirati.
Trošak životnog vijeka pumpnog agregata
Trošak životnog vijeka pumpe temeljem matematičke analize daje procjenu postojećeg stanja te uvid u potencijalna optimalna rješenja za povećanje životnog vijeka agregata i postizanje veće iskoristivosti stroja. Analiziraju se dva ili više konstrukcijski istih ili dovoljno sličnih agregata. Treba pripaziti da se promatraju isti konstrukcijski ili procesni parametri. Trošak životnog vijeka pumpe predstavlja ukupan trošak nabave, ugradnje, rada, održavanja, nabave i skladištenja rezervnih dijelova, popravaka, generalnih servisa, utjecaja na okoliš i zbrinjavanja opreme.
Određivanje troška životnog vijeka obuhvaća metodologiju kojom određujemo i kvantificiramo sve nabrojene troškove. Trošak životnog vijeka možemo koristiti za procjenu isplativosti nove pumpe u usporedbi s troškom generalnog servisa postojeće pumpe identičnih karakteristika, procjenu vrste održavanja te isplativosti kroz buduće vremensko razdoblje.
Trošak životnog vijeka pumpnog agregata računa se po formuli:
Tz = Tic + Tin + Te + To + Tm + Ts + Tenv + Td
pri čemu je:
Tz …Trošak životnog vijeka pumpe
Tic …trošak nabave/kupovine agregata, strojnog sustava, pomoćnog sustava
Tin … trošak ugradnje i puštanja u rad, uključujući obuku djelatnika
Te … trošak energenata, procjenjeni trošak potrošnje energenata kada je sustav u radu, uključujući pogonski stroj, opremu za praćenje rada te pomoćni sustav
To … trošak rada agregata, obuhvaća normalan svakodnevni nadzor rada
Tm … troškovi rutinskog održavanja i popravaka temeljem prediktivnog državanja
Ts … troškovi zastoja (gubitka proizvodnje zbog kvara)
Tenv … troškovi onečišćenja okoliša radi izlijevanja radnog medija npr.zbog propuštanja brtvenice ili pomoćnog sustava brtvljenja
Td … troškovi zbrinjavanja na kraju životnog vijeka, uključujući radove demontaže
Sada ćemo detaljno razraditi svaki tip troškova kako bismo dobili cjelovitu računicu.
Trošak nabave pumpnog agregata i/ili strojnog sustava, Tic
Prilikom projektiranja proizvodnog postrojenja projektant mora odlučiti o prostornom planu svih strojnih sustava. Pumpni agregati su povezani cjevovodima, što je manji promjer cijevi i armature to će biti niži trošak nabave i ugradnje čitavog sustava. Međutim, cjevovodi manjih promjera moraju biti spojeni na pumpe veće snage koje će davati veći tlak, što rezultira skupljim pumpama. Manji promjer cijevi na usisnoj strani pumpe rezultira nižom neto pozitivnom usisnom visinom. Tijekom faze projektiranja javit će se i drugi izbori koji mogu utjecati na početno ulaganje u izgradnju procesnog postrojenja, počevši od kvalitete izabrane opreme.
Različiti materijali od kojih je izrađena oprema i strojevi imaju različite brzine trošenja, različite mogućnosti podnošenja radnog opterećenja i utjecaja radnih medija, pogotovo u kemijskoj i naftnoj industriji. Različiti tipovi strojeva mogu imati različite troškove nabave, ali u konačnici dovesti do manjeg troška ukupnog životnog vijeka. Početna ulaganja uključuju još troškove projektiranja, administraciju nabave, testiranja i inspekcijske preglede, proces nabave, obuku djelatnika, rezervne dijelove za pokretanje i dvogodišnji rad te pomoćnu opremu za nadzor, upravljanje, hlađenje i brtvljenje.
Trošak ugradnje, puštanja u rad i obuke djelatnika, Tin
Trošak ugradnje prosječnog pumpnog agregata i njegovo puštanje u rad obuhvaća troškove betoniranja temeljne ploče, montažu nosača i pričvršćivanje sidrenim vijcima na temelje te podlijevanje betonom ili epoksi smjesom, spajanje usisnih i tlačnih cijevi, montažu usisnih, tlačnih i regulacijskih ventila, spajanje električnih kabela, spajanje instrumentalnih kabela i instrumentalnih uređaja, spajanje pomoćnih sustava, ispiranje strojnog sustava prije puštanja u rad radi uklanjanja nečistoće i ispitivanja nepropusnosti, analizu učinkovitosti pri prvom puštanju u rad te potrebna podešavanja, dotezanja i prilagodbe sustava nakon puštanja u rad. Ugradnju može izvesti dobavljač opreme, podizvoditelj ili djelatnici matične kompanije. Izbor izvoditelja radova utječe na trošak radne snage, vještinu radne snage, dostupnost alata i uređaja za izvođenje radova.
Ugradnja uključuje još i transport opreme i strojeva, postavljanje na predviđena mjesta prema prostrnom planu postrojenja, spajanje sustava, nadzor radova te obuku djelatnika. Pokretanje strojeva mora biti prema uputama proizvođača i izvodi se uz prisustvo predstavnika proizvođača i/ili dobavljača. Pritom treba ispuniti kontrolne liste radi provjera funkcionira li oprema unutar određenih parametara. Nakon uspješnog završetka faze puštanja u rad sve uključene strane potpisuju primopredajni zapisnik.
Trošak potrošnje energenata u mirovanju, radu te za pomoćne sustave, Te
Potrošnja energije je jedan od najvećih troškovnih elemenata u ukupnom trošku životnog vijeka stroja, pogotovo ako pumpa radi više od 2500 sati godišnje. Snaga pumpe računa se po formuli:
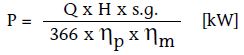
pri čemu je
Q…. protok
H …. visina dobave
ηp … učinkovitost pumpe
ηm … učinkovitost elektromotora/pogonskog stroja
s.g. … specifična gustoća radnog medija
Projektant postrojenja mora imati zasebne podatke za svaki pumpni agregat ili strojni sustav u odnosu na ukupnu učinkovitost rada. Učinkovitost se može promatrati kao ukupna učinkovitost pojedinog pumpnog agregata ili kao ukupna količina energije koju je sustavu utrošio u različitim režimima rada. Izbor pogonskog stroja utječe na količinu utrošene energije. Npr., više struje se koristi za pogon pumpe klasičnim elektromotorom nego elektromotorom sa frekventnim pretvaračem. K tome, ponekad potrošnja energije ne ovisi o radnom opterećenju, npr. kada sustav upravljanja sam podešava konstantno energetsko opterećenje dok varijabilni elektromotor troši različitu količinu energije pri različitim radnim opterećenjima.
Primjena prigušnih ventila, prekotlačnih ventila ili mjernih blendi za kontrolu rada će smanjiti učinkovitost i povećati količinu potrošene energije. Također, treba uključiti trošak energije i materijala potreban za rad pomoćnih sustava, poput troškova grijanja i hlađenja, sustava ispiranja te sustava brtvljenja. Npr. pomoćni sustav hlađenja uključuje trošak pripreme rashladne vode, pumpe, filtera te izmjenjivača i armature.
Troškovi rada agregata uz svakodnevni nadzor, To
Troškovi rada ovise o kompleksnosti i svrsi sustava prepumpavanja. Npr., pumpa koja se koristi za pumpanje sirove nafte treba biti više puta provjeravana tijekom dana radi propuštanja, pouzdanog rada i odgovaraju li radni parametri potrebama proizvodnog procesa. S druge strane, pumpa za prepumpavanje pročišćene vode u automatiziranom sustavu treba vrlo malo ili nimalo nadzora tijekom rada. Redovito praćenje rada daje informaciju operaterima o potencijalnim gubicima u sustavu pumpanja. Ključni pokazatelji rada pumpnog agregata su promjene brzine vibracija, neuobičajene promjene temperature, razine buke, povećanje/smanjenje potrošnje energije, količina protoka i tlak radnog medija na tlačnoj strani.
Troškovi rutinskog održavanja i popravaka temeljem prediktivnog održavanja, Tm
Održavanje optimalnog radnog vijeka pumpe zahtijeva redovito održavanje i servisiranje. Proizvođači agregata daju preporuke o učestalosti i kompleksnosti rutinskog održavanja. Troškovi rutinskog održavanja ovise o učestalosti, opsegu i količini utrošenog materijala. Konstrukcija pumpe utječe na trošak materijala, izbor rezervnih dijelova te trajanje servisa. Program održavanja može biti planiran tako da se vrše skuplji servisi tijekom duljih vremenskih intervala ili da se provode jednostavne aktivnosti tijekom kraćih vremenskih intervala. Tijekom servisnih radova pumpa je demontirana s radne pozicije u postrojenju i prevezena u mehaničarsku radionicu.
Tijekom trajanja radova u radionici smanjuje se pouzdanost procesnog postrojenja i mogući su gubici u proizvodnji ako pumpa nema zamjensku poziciju. Troškovi servisa mogu biti smanjeni tako da se godišnje planira raspored servisa tijekom perioda kada je procesno postrojenje u obustavi ili u remontu.
Ukupan trošak rutinskog održavanja se dobije kada pomnožimo trošak pojedinačnih aktivnosti s brojem izvršenih aktivnosti održavanja tijekom očekivanog radnog vijeka pumpe. Iako ne možemo predvidjeti točan broj neočekivanih ispada ili kvarova, izračunavši srednji period između kvarova (MTBF) možemo dobiti prihvatljivu procjenu. MTBF se može procijeniti za pojedinačne dijelove pumpe i potom kombinirati da dobijemo konačan broj za čitav agregat. Ponekad je dovoljno razmotriti najbolji i najgori mogući scenarij „što ako“ za slučaj najkraćeg trajanja životnog vijeka i za slučaj najduljeg životnog vijeka temelj povijesnih podataka o radu stroja zabilježenih u računalnom sustavu za upravljanje održavanjem CMMS.
Proizvođači agregata mogu odrediti i dati informacije o MTBF za dijelove čiji kvarovi obustavljaju rad pumpe i skraćuju njen životni vijek ispod prihvatljivog trajanja. Vrijednosti MTBF se dobiju analizom povijesnih podataka ili pomoću matematičkih modela. Vrijednosti se najčešće odnose na vijek trajanja brtvenice, ležajeva, vratila, spojke i potrošnih prstena. MTBF vrijednosti se mogu usporediti s očekivanim vijekom trajanja i izračunatim brojem kvarova promatranog agregata. Ipak, moram vas upozoriti da često proizvođači strojeva nisu baš voljni pružiti ovakvu vrstu podataka kada im pošaljete upit. Na MTBF također utječu radni parametri proizvodnog procesa te načini rukovanja strojem.
Troškovi zastoja/gubitka proizvodnje, Ts
Trošak neočekivane obustave proizvodnog procesa i gubici proizvodnje imaju značajan udio u trošku životnog vijeka stroja. Unatoč očekivanom životnom vijeku definiranom u fazi konstruiranja stroja, u stvarnosti će prije ili poslije doći do neočekivanih havarija. U slučajevima havarija kada je gubitak proizvodnje neočekivano visok, često se ugrađuje rezervni pumpni agregat kako bi se smanjio rizik. Ako imamo raspoloživ rezervni pumpni agregat, početni troškovi će biti veći, ali trošak neplaniranog popravaka radi havarije će uključivati samo rad mehaničara i rezervne dijelove jer ćemo izbjeći neplanirane gubitke proizvodnje.
Troškovi čišćenja okoliša nakon izlijevanja radnog medija, Tenv
Troškovi sanacije onečišćenja okoliša tijekom životnog vijeka pumpnog agregata ovise o vrsti radnog medija koji se prepumpava i izlije u okoliš zbog neočekivanog propuštanja. Određeni radni mediji manje onečišćuju okoliš u usporedbi s drugima, ali imaju veće troškove proizvodnje. Neki primjeri onečišćenja okoliša nastali zbog kvara pumpnog agregata su propuštanje rashladne vode iz sustava brtvljenja zbog oštećenja mehaničke brtvenice, izlijevanje korozivnih ili toksičnih radnih medija, propuštanje ulja za podmazivanje uslijed oštećenja brtvenog prstena na ležajnom kućištu te propuštanje na kućištu radi pukotina. Ovdje treba uključiti i godišnje troškove nadzora inspekcijskih tijela, obnavljanej vodopravne dozvole i sl.
Troškovi zbrinjavanja i demontaže na kraju životnog vijeka, Td
U većini slučajeva, troškovi zbrinjavanja pumpnog agregata imaju male varijacije u iznosu, bez obzira na konstrukciju pumpe te vrstu radnog medija koji je prepumpavala. Trošak demontaže i zbrinjavanja pumpe za prepumpavanje otpadne vode i pumpe za prepumpavanje glicerina su jednaki. Iznimka su slučajevi kada radni medij podliježe posebnim zakonskim regualtivama poput toksičnih ili radioaktivnih tvari. Tada se trošak demontaže i zbrinajvanja može povećati nekoliko puta radi posebnih uvjeta koje treba ispunjavati i tako u konačnici uvećati ukupan trošak životnog vijeka agregata.
Ukupan trošak životnog vijeka
Procijenjeni troškovi različitih elemenata koji čine životni vijek pumpnog agregata moraju biti izračunati tako da ih je moguće uspoređivati s troškovima različitih tipova konstrukcije pumpi. Najjednostavnije i najpreglednije je pomoću tablice. Za elemente kojima nije moguće izračunati konkretnu vrijednost treba upisati objašnjenje. Napominjem da je u razmatranje troškova potrebno provjeriti i razmotriti postojeće troškove energenata, očekivane godišnje stope inflacije za cijene energenata tijekom životnog vijeka agregata, kamatne stope, očekivane rabate te trošak amortizacije.
Za kraj današnjeg članka, ovdje je mali šalabahter sa smjernicama za smanjenje troška životnog vijeka pumpnog agregata:
- redovito primjenjujte preventivno održavanje,
- prilikom svakog servisa pumpe provjerite unutarnje zračnosti među dijelovima,
- prilikom nabave novog agregata vodite se principima troškova koje smo ovdje naveli,
- provjerite imate li prisutan gubitak energije zbog regulacijskih ventila,
- racionalno koristite pomoćne sustave,
- nemojte nabaviti prekapacitiranu/podkapacitiranu pumpu,
- odaberite pumpu i pogonski stroj prema potrebnoj namjeni i radnom mediju,
- nabavite visoko učinkovit elektromotor,
- vodite računa da imate odgovarajuću spojku ili reduktor,
- analizirajte postojeće sustave pumpnih agregata i provjerite gdje imate mogućnosti za poboljšanja,
- provjerite postoje li načini za optimizaciju troškova postojećih agregata,
- provjerite odgovaraju li postojeći agregati zahtjevima prepumpavanja u uvjetima rada proizvodnog procesa te
- uvijek nastojite pratiti učinkovitost rada postojećeg sustava i tu ćete naći prve mogućnosti za poboljšanja.
Znate li izračunati trošak pumpnog agregata tijekom njegovog životnog vijeka? Koje metode ste koristili? Koje parametre ste uključili u izračun? Podijelite svoja iskustva u komentarima!