Remeni su glavni element remenskog prijenosa gibanja kod određenih tipova rotacijske opreme poput ventilatora zračnih hladnjaka ili puhala zraka. Prema istraživanjima, više od 84% klinastih i zupčastih remena prikazanih na slici 1. nikada ne ispuni predviđeni radni vijek zbog nepravilne montaže, neodgovarajućeg tipa ili krivog skladištenja.
Posljedice takvih situacija su neočekivani prekidi u radu rotacijske opreme zbog pucanja ili skliznuća remena, gubitak kapaciteta i povećanje troškova zbog zastoja u proizvodnom procesu ili visoke potrošnje električne energije. Danas razmatramo preporuke dobre prakse za rukovanje, montažu i korektivno održavanje remenskog prijenosa.
Slika 1.: Klinasti i zupčasti remen
Za početak, pridržavajte se svih propisanih sigurnosnih mjera i koristite osobna zaštitna sredstva. Kada uzimate nove remene u skladištu provjerite duljinu remena, odnosno pripazite da ste izabrali jednak set za jedan stroj. Bilo je slučajeva kada je isti (ne baš vrhunski) proizvođač isporučio različite remene za isti stroj.
Prilikom demontaže olabavite temeljne vijke elektromotora pogonskog stroja te ga pomaknite sve dok postojeći remeni ne budu labavo visili i potom ih uklonite bez primjene sile. Nasilno čupanje remena može uzokovati ozljede te oštetiti remenice. Iz istog razloga nemojte odvijačem izbacivati remene iz remenica.
Nakon uklanjanja remena detaljno ga pregledajte po cijeloj dužini s vanjske i unutarnje strane. Nejednolika istrošenost na pojedinom dijelu unutarnje strane ukazuje na problem u konstrukciji remenice ili manjak održavanja. Ako je riječ o manjku održavanja, u ovom članku ćete naći smjernice za preventivno održavanje.
Vizualno kontrolirajte i zamijenite remenicu ako ima tragove jakog trošenja, hrđe, napuknuća, dubinskih pukotina ili savijene strane utora. Utori koji se sjaje ili izgledaju ispolirano također ukazuju na trošenje materijala. Nemojte čistiti remenicu pjeskarenjem ili brušenjem pomoću ručne brusilice jer ćete tako dodatno ukloniti materijal s već istrošene površine remenice, što će kasnije dovesti do bržeg trošenja i pucanja remena ili pojave dubokih pukotina na remenici. Izmjerite dubinu utora na remenici da biste provjerili kolika je istrošenost te ako je potrebna zamjena remenice. Ukupno trošenje materijala u dubini pojedinog utora ne bi trebalo biti veće od 0.8 mm.
Remeni i remenice moraju biti centrirani po mogućnosti korištenjem uređaja za lasersko centriranje. Proizvođači remena preporučuju dopušteno odstupanje prilikom centriranja do max. 0.5°. Također prije centriranja provjerite u korisničkom priručniku stroja kolika odstupanja su dozvoljena. Kada se centriraju remenice, postavite laserski uređaj na manju remenicu i prema njoj centrirajte veću remenicu što je prikazano na slici 2. Laserski uređaj mora pokazati centriranost u sva 3 stupnja slobode – aksijalno, kutno horizontalno i kutno zakrenuto.
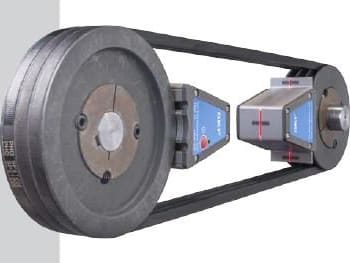
Slika 2. Lasersko centriranje remenica
Kada na remenici treba mijenjati 2 ili više remena, tada zamijenite sve remene odjednom novim remenima istog proizvođača. Nikada nemojte mijenjati samo jedan a prestale remene ostaviti postojeće. Takva situacija dovodi do nejednolikog rasporeda opterećenja i preuranjenog trošenja remena ili remenice. Kada montirate novi remen, provjerite da remeni i utor na remenici međusobno odgovaraju. Nemojte na silu nastojati ubaciti remen u utor remenice niti koristiti odvijač u tom postupku jer ćete tako oštetiti remen, remenicu ili oboje.
Kada je remen montiran, krenite pomicati elektromotor sve dok remen ne bude zategnut. Prethodno treba provjeriti nožice elektromotora za prisutnost soft foota. Ako je soft foot prisutan, prvo ga otklonite a potom nastavite s radom na remenima. Očitanje postojećeg otklona elektromotora ne smije biti veće od 0.05 mm.
Koristite tenziometar i provjerite je li napetost remena u skladu sa specifikacijama. Postoje drugi, moderniji i skuplji uređaji za provjeru nategnutosti remena, ali neki od njih nisu dozvoljeni za rad u zoni opasnosti od eksplozije. Po potrebi provjerite kod proizvođača remena koje su dozvoljene vrijednosti napetosti remena ovisno o radnom opterećenju stroja. Odgovarajuća napetost remena je minimalno potrebna vrijednost da bi se spriječilo skliznuće remena s remenice pri maksimalnom radnom opterećenju.
Ako nemate dostupne podatke, možete koristiti tenziometar na način da ga zakačite na sredinu duljine remena i onda potegnete prema dolje, što je prikazano na slici 3. Pritom pratite koliki je progib i zabilježite ga kao što je prikazano na slici 4. Remeni moraju biti napeti toliko koliko je potrebno da sila potrebna za povlačenje remena bude jednaka maksimalno dozvoljenoj sili koju propisuje proizvođač za montirani remen.
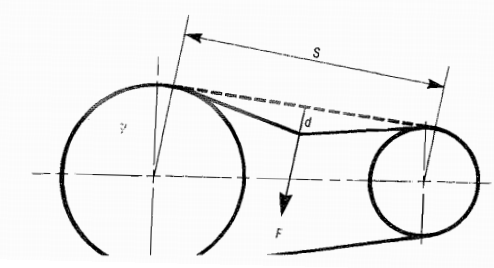
Slika 3. Djelovanje sile na remen radi provjere napetosti i nastalog progiba
Rukom okrenite remenicu nekoliko puta u smjeru vrtnje elektromotora i po potrebi podesite nategnutost remena. Još jednom provjerite nalijeganje remena u utorima remenice i po potrebi ga podesite. Sada treba dotegnuti temeljne vijke elektromotora prema specificiranom momentu, pogledajte u dokumentaciji stroja koja je propisana vrijednost momenta.
Na kraju treba montirati zaštitni poklopac preko remenskog prijenosa. Tek sada se elektromotor može spojiti na izvor napona i stroj pokrenuti u rad. Nakon toga poslušajte i prekontrolirajte je li prisutna neuobičajena buka, povećane vibracije ili pregrijavanje. Možda će biti potrebno podmazivanje, ponovno dotezanje ili popuštanje remena te provjera centriranja da bi se osigurao pravilan rad.
Zapišite u dokumentaciju stroja datum zamjene remena, tip i broj remena, opišite ukratko stanje starih remena, navedite razlog zamjene (npr. redovna zamjena, preventivno održavanje i sl.). Nakon svakog centriranja popunjava se protokol o obavljenom poslu, za kritične strojeve je protokol obavezan dok se za nekritične strojeve ispunjava nakon generalnog servisa. Na slici 4. je primjer protokola o centriranju gdje se upisuju vrijednosti centriranja, sila i izmjeren progib.
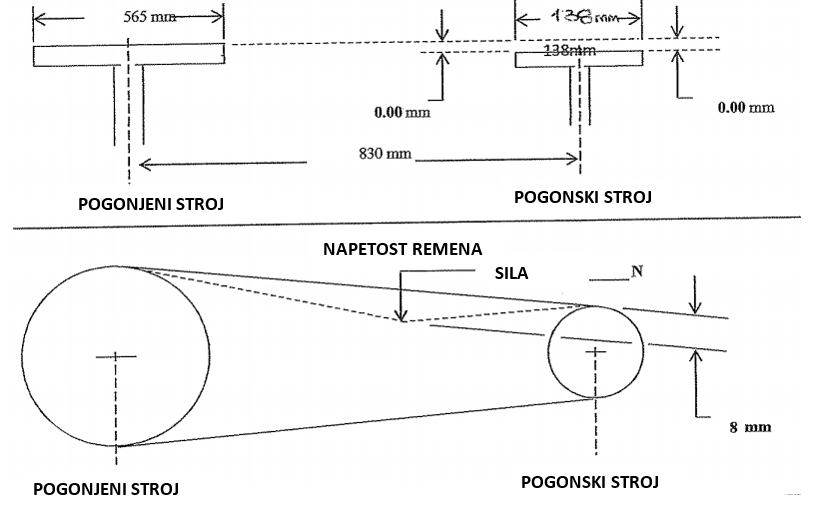
Slika 4. Protokol o centriranju i izmjeren progib
Proizvođači remena na svojim web stranicama imaju aplikaciju za provjeru. Na linku vam je jednostavan kalkulator za izračun napetosti remena, samo ćete morati preračunavati mjerne jedinice iz imperijalnih u SI jer se radi o američkom proizvođaču.
Remeni ne bi trebali proizvoditi iritirajući zvuk cviljenja kada se stroj pokrene u rad ako su odgovarajuće dotegnuti. Zvuk cviljenja je znak da remeni ne odgovaraju, nisu odgovarajuće postavljeni u utore remenica ili nisu odgovarajuće dotegnuti a ponekad je u pitanju kombinacija svega navedenog.
Kod nekih remena potrebna je razrada ili uhodavanje tijekom određenog vremena kako bi remen u potpunosti nalegao u utor remenice i radi postizanja pouzdanog rada. Tada se preporučuje zaustaviti stroj te provjeriti i dotegnuti remen nakon što je stroj radio pri punom radnom opterećenju 30 min, 24h i 48h. Svakako provjerite u dokumentaciji stroja ili konzultirajte proizvođača remena ako imate ovakav slučaj.
Proračun za provjeru napetosti remena
Napetost remena ili dotegnutost se provjerava djelovanjem sile i mjerenjem ili računanjem progiba remena prikazanog na slici 3.
Sila potrebna za dotezanje remena se računa po formuli:
F = (P X 50) / v
pri čemu je
F – sila, N
P – snaga pogonskog stroja, kW
v – brzina klizanja remena po remenici, m/s
Brzinu računamo na način
v = (S X N X n) / 60000
S – udaljenost između središta dviju remenica prikazana na slici 3, mm
N – broj utora u remenici
n – brzina vrtnje pogonskog stroja, rpm
Minimalna sila dotezanja remena se računa po formuli
F = (P X 25) / v
Dozvoljeni progib remena d se računa po formuli:
d = S / 50
Uzmimo za primjer elektromotor snage 60 kW, brzine vrtnje 2500 rpm, koji pokreće ventilator. Remenice oba stroja imaju 3 utora, tj. pogonski i pogonjeni stroj su povezani remenskim prijenosom koji čine 3 remena. Udaljenost središta dviju remenica će biti 1750 mm.
Brzina klizanja remena će biti:
v = (S X N X n) / 60000
v = ( 1750 X 3 X 2500) / 60000 = 2187,5 mm/s = 2,2 m/s
Minimalna sila dotezanja iznosi:
F = (P X 25) / v
F = (60 X 25) / 2,2 = 682 N
Sila dotezanja iznosi:
F = (P X 50) / v = (60 X 50) / 2,2 = 1363,6 N
Dozvoljeni progib remena za navedene parametre će biti:
d = S / 50 = 1750 / 50 = 35 mm
Kako provjeravate dotegnutost remena? Koje probleme ste imali s remenskim prijenosom? Podijelite vaša iskustva u komentarima!