Proces rutinskog održavanja strojeva i opreme je dio svakodnevnog poslovanja u proizvodnim i procesnim postrojenjima. Proces uključuje proaktivno(prediktivno i preventivno) i reaktivno održavanje (popravci). Djelatnici uključeni u proces su inženjeri iz održavanja, operateri iz postrojenja iz djelatnici iz radione podijeljeni po strukama (električari, mehaničari, instrumentalci i sl.) te po potrebispecijalisti iz različitih područja.Ovisno o veličini postrojenja i broju strojeva uvijek postoji određen broj djelatnika koji rade zajedno i dijele resurse te koordiniraju posao ovisno o prioritetima.
Od svih tipova održavanja, rutinsko održavanje je najteže ostvarivati uz visoku razinu kvalitete i efikasnosti kroz dulje vrijeme zbog brojnih razloga: ovisnost o pojedincima koji donose odluke kada je u pitanju sadašnji rizik u odnosu na dugoročni doprinosu, nedovoljna obučenost djelatnika, uključenost velikog broja djelatnika s različitih strana, različitost prioriteta koji su si međusobna konkurencija, kompanije koje nagrađuju djelatnike što se iz dana u dan bave vatrogasnim rješavanjem situacija, ponavljanje poslova iz dana u dan koji se ne završavaju na vrijeme, hitnoće koje prekidaju planirane radove i ruše rasporede, djelatnicima koji imaju slabije tehničke vještine se dodjeljuju jednostavniji ponavljajući poslovi dok vještiji djelatnici rade na kompleksnijim poslovima ili rješavaju hitnoće.
Osnovni organizacijski preduvjeti za ostvarivanje rutinskog održavanja su postojanje službe koja obavlja održavalačke radove tijekom osmosatnog radnog vremena, prijavljivanje hitnih kvarova odmah na početku radnog vremena čime se prekidaju ili pomiču tekući radovi, rješavanje hitnih kvarova sve do završetka posla i puštanja stroja u rad, odrađivanje visoko prioritetnih planskih radova po potrebi i vikendom. Danas ćemo razmotriti koji su osnovni elementi u procesu rutinskog održavanja i rješavanja popravaka. Na slici 1. su navedeni svi elementi svakodnevnog rutinskog održavanja.
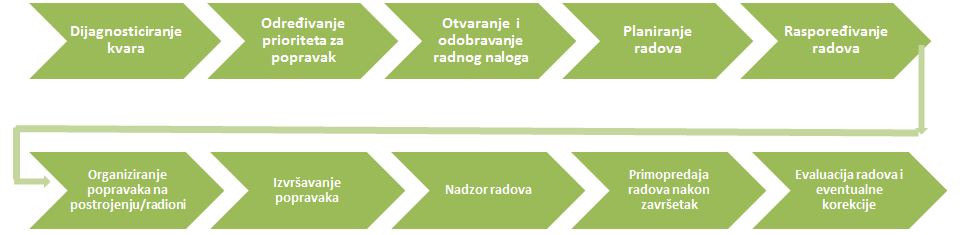
Slika 1. Elementi procesa rutinskog održavanja
Krenimo redom:
Obavijest o zastoju stroja i dijagnostika kvara
U većini slučajeva djelatnik službe održavanja koji obavještava o zastoju stroja i nastalom kvaru treba napraviti dijagnostiku ili ako je djelatnik operater na proizvodom postrojenju pa nije u potpunosti siguran o kojoj vrsti kvara se radi, tada treba obavijestiti djelatnika iz službe održavanja da dođe dijagnosticirati kvar. Kod kompleksnih strojnih sustava ponekad je čak potrebno pozvati specijaliziranu tvrtku koja se bavi specifičnom vrstom dijagnostike.
Kvar znači da stroj ne obavlja više svoju funkciju za koju je namijenjen ili da njegov rad odstupa od uobičajenog, npr. pumpa nema dobave, kompresor ne uspijeva postići 100% kapaciteta, glava ventilatora ima povećane vibracije, na reduktoru se učestalo uključuje alarm povišene temperature ulja i sl. Nakon dijagnostike kvara otvara se prijava koja mora sadržavati: datum i vrijeme nastanka kvara, tehnološku oznaku stroja, konkretan i sažet opis kvara, posljedice kvara na proizvodnju (onečišćenje okoliša, gubitak proizvoda, ispad postrojenja, i sl.) i uvjete u kojima stroj radi (radni medij, tlak, temperatura te ostali potrebni detalji).
Određivanje prioriteta i raspoređivanje
Određivanje prioriteta za izvršavanje popravaka i vremensko raspoređivanje radova su dva elementa koji se planiraju zajednički te odgovaraju na pitanja a) Koji kvarovi su hitnoće i moraju biti riješeni čim prije? i b) Ako kvar nije hitan, u kojem vremenskom roku mora biti otklonjen?
Ako su svi kvarovi hitni, tada se stvara preopterećenje sustava i resursa uz veće troškove. Zato treba provjeriti opravdanost svake hitnoće i ako je moguće što više kvarova otklanjati u duljem vremenskom periodu. Osim hitnih kvarova, postoje još kvarovi koji imaju prioritet otklanjanja u periodu od svega nekoliko dana, do dva tjedna, do mjesec dana ili do nekoliko mjeseci ako je riječ o planiranim polugodišnjim/godišnjim servisima. Računalni sustavi za upravljanje održavanjem (CMMS) imaju odabir prioriteta otklanjanja kvara u izborniku.
Planiranje i izvršavanje radova
Sljedeći logičan korak je planiranje radova za otklanjanje kvarova. Neplanirani radovi za otklanjanje kvarova i promašaji u određivanju prioriteta uzimaju do 4 puta više vremena i resursa u usporedbi s planiranim radovima i prethodno određenim prioritetima. Glavni cilj bi trebao biti postizanje što većeg broj planskih radova prema određenim prioritetima. Obilježja planiranih radova su svi potrebni resursi (alat, materijal, rezervni dijelovi, djelatnici po strukama, inertizacija, dreniranje, dozvole za rad, blindiranje, prateća mehanizacija, transportna sredstva ) u predviđeno vrijeme na predviđenom mjestu tako da se kvar može u potpunosti otkloniti bez prekidanja posla od početka do kraja.
Raspored izvršavanja radova mora biti posložen tako da nema praznog hoda i nepotrebnih produljivanja. Prije planiranja radova treba pregledati mjesto rada gdje se stroj nalazi, koji su svi pripremni radovi i resursi potrebni ovisno o tome hoće li se popravak izvršiti u radioni ili na postrojenju te procijenjeno vrijeme za radnje prije puštanja stroja u rad nakon dovršetka popravka (deblindiranje, vraćanje izolacije, punjenje radnim medijem, odzračivanje i sl.) Tijekom planiranja radova obavezno treba navesti je li za izvođenje radova potrebna skela, transportna sredstva (dizalica, kamion, viljuškar…), posebna zaštitna sredstva itd.
Potom se sastavlja radni nalog u kojem se navodi redoslijed radova uz prateće resurse, alat, popis materijala, transportna sredstva i sve potrebne struke. Radni nalog se šalje svi uključenim djelatnicima, tj. nadzornim inženjerima i sprema u CMMS tako da bude dostupan kad god je potrebno.
Evaluacija, mjerenje i prilagođavanje procesa
Nakon kompleksnih i dugotrajnih popravak i mukotrpnog puštanja stroja u rad, većini održavatelja je jednostavno drago da je posao konačno gotov i da mogu ići dalje s popravcima drugih strojeva (koliko puta ste bili u ovakvoj situaciji? 😉 ). Umjesto da stanemo, zapitamo se zašto je bilo toliko teško i mukotrpno, mi smo jednostavno sretni što možemo to ostaviti iza sebe i od sutra krenuti s radom na drugim strojevima.
Podrobnija analiza bi nam ukazala na sve propuste i nepravilnosti, međutim zbog preopterećenosti poslom, brojnih obaveza i drugih smetnji ovakav pristup je nažalost postao prije pravilo nego iznimka kod većine djelatnika u održavanju u velikom broju kompanija. Brojni poslovni procesi imaju evaluacijske formulare kao standardni dio poslovanja nakon odrađenog projekta ili aktivnosti temeljem kojih se točno određuje koji koraci su uzrokovali kašnjenja ili gubitke, međutim u praksi svakodnevnog rada jednostavno nemamo vremena ili resursa da se dodatno bavimo ovakvim analizama.
Čak i kada se u rutinski proces održavanja nastoji uvesti evaluacija procesa nakon otklanjanja kvara, često se ovakva dobra namjera pretvori u dodatnu papirologiju koja zahtijeva sudjelovanje puno ljudi i dodatno opterećenje uz ionako pretrpan raspored.
Evaluacija bi trebala omogućiti djelatnicima izvještavanje o svim situacijama koje nisu bile u skladu s predviđenim procedurama i o svim negativnostima što su dovele do kašnjenja ili gubitaka kako bi se ubuduće radilo efikasnije i naučilo na prethodnim greškama.
Evaluacija treba ukazati na postotak neplaniranih radova koji su se pojavili, postotak dodatnih radova koji su se pojavili u postupku defektaže, postotak radova koji us bili u skladu s planiranim, usporedbu planiranog i ostvarenog rada, materijala i resursa. Evaluacija bi trebala biti napravljena svakog ponedjeljka za prethodni tjedan, bilježiti sve nepravilnosti da se može vidjeti koji krivi koraci se ponavljaju i kako ih ispraviti ili eliminirati te poboljšati planiranje ubuduće. Tako kontinuirano unaprijeđujemo proces rutinskog održavanja strojeva i opreme.
Završni korak je prilagođavanje procesa rutinskog održavanja temeljem provedene evaluacije. Svako povećanje efikasnosti zahtijeva neprestano prilagođavanje zato što se u praksi održavalačkog posla nije desilo da imate dva identična tjedna zaredom po pitanju količine potrebnih resursa, materijala ili radova. Ako je količina potrebnih resursa u radioni ili na postrojenju identična iz dana u dan, znači da ih imate ili premalo na raspolaganju ili previše. Ako ih imate premalo, povećava se rizik, a ako ih imate previše znači da upravljanje resursima nije učinkovito koliko bi trebalo biti.
Kakav je vaš proces rutinskog održavanja strojeva? Provodite li redovite evaluacije? Što ste naučili i koje propuste ste uočili? Podijelite vaša iskustva u komentarima tako da svi naučimo!
Pitanja, komentare i poruke šaljite na mail: katarina_knafelj@hotmail.com