Podaslov današnjeg članka je ujedno – 16 Pitanja o ISO standardima koja niste imali kome postaviti. ISO 55000 je međunarodna norma izdana 2014. godine koja pruža model za razvoj, implementaciju i održavanje sustava upravljanja imovinom (strojevima, opremom, zgradama i svom ostalom fizičkom imovinom koja zahtijeva održavanje, upravljanje i praćenje kako bi ispunjavala svoju funkciju i donijela korist).
Norma ISO 55000 se sastoji od:
ISO 55000 Upravljanje fizičkom imovinom – Pregled, principi, terminologija
ISO 55001 Upravljanje fizičkom imovinom – Sustav upravljanja – Zahtjevi
ISO 55002 Upravljanje fizičkom imovinom – Sustav upravljanja – Smjernice za primjenu ISO 55001
ISO 55000 i ISO 55002 sadrže opisan sustav i smjernice za upravljanje imovinom, dok ISO 55001 definira zahtjeve.
U svakodnevnoj komunikaciji često dolazi do zabune jer se spominje “ISO 55000” dok se u stvari misli na ISO 55001 i 55002 koji su nama posebno zanimljivi sa stajališta održavanja strojeva, strojnih sustava i opreme u procesnim i proizvodnim postrojenjima.
U današnjem članku donosim detaljan pregled i i iscrpna pojašnjenja što su norme ISO 55000, čemu služe, kako ih implementirati, kada i gdje te prednosti koje donose. Za uvođenje sustava upravljanja imovinom i certifikaciju potrebna su vam sva 3 standarda jer se međusobno nadovezuju i nadopunjuju.
Standard ISO 55000 je krovni dokument i daje generalni pregled za uvođenje sustava upravljanja imovinom. Namjena mu je pružiti jasno i strukturirano rezumijevanje principa i zahtjeva koje treba primijeniti.
Uvođenje svih elemenata norme ISO 55000 slijedi definiranu metodologiju i procese koji čine sustav upravljanja imovinom, pruža integriranu strukturu i uspostavlja povezanost među svim elementima.
Osnovni koraci u primjeni norme ISO 55000 su:
- Smjernice: Standard kombinira smjernice i politike upravljanja imovinom te utvrđuje načela kojih se treba pridržavati kompanija ili organizacije kako bi uskladila ciljeve upravljanja s poslovnim ciljevima.
- Ciljevi: Upravljanje ciljevima mora biti specifično, mjerljivo, dostižno, realno i u vremenskom roku (SMART: Specific, Measurable, Attainable, Realistic and Time-bound) uz procjenu kategorija poput produktivnosti imovine, održivosti, sukladnosti sa regulativama, životnog ciklusa te racionalizacije troškova.
- Strategije: pokazuju kako će se poslovni ciljevi promijeniti u ciljeve sustava upravljanja imovinom, definiranje procesa i rokova koje treba dostići
- Dokumentacija: sve aktivnosti sustava upravljanja imovinom moraju biti dokumentirane, uključujući planove proizvodnje i održavanja, kapitalne investicijske planove (revizije, nadogradnje, zamjene i revitalizacije) i resurse. Dokumentacija se mora periodično provjeravati i nadopunjavati radi usklađivanja s ciljevima.
- Vodstvo: menadžment treba poduprijeti i odobriti strategiju upravljanja imovinom postavljanjem rokova, primjene i odgovornosti. Treba odrediti zaposlenike koji će koordinirati razvoj, implementaciju, rad i kontinuirano poboljšanje sustava upravljanja imovinom, međutim direktori i vlasnici snose punu odgovornost za provedbu.
- Planiranje: procjena svih kratkoročnih i dugoročnih rizika te kako će se sustav upravljanja imovinom integrirati u druge poslovne procese
- Podrška: definira potrebne resurse i zaposlenike, povezuje sve sudionike i proširuje doseg komunikacije među različitim odjelima kompanije
- Poslovanje: procjenjuje se implementacija, kontrola poslovnih procesa, prate se rizici i podupire uvođenje potrebnih promjena
- Procjena: identificira metriku za praćenje financijskih pokazatelja sustava upravljanja imovinom i obavlja provjere sukladnosti
- Poboljšanja: korigiraju se otkrivene nesukladnosti i uspostavlja kontinuirano unaprijeđenje
Standard ISO 55001 je model za razvoj sustava upravljanja imovinom koji određuje zahtjeve. Kada detaljnije proučimo standard, vidimo da su zahtjevi poprilično generički jer se primjenjuju na različite tipove tvrtki.
Pojednostavljeno govoreći, ISO 55001 kaže što moramo napraviti, ne kako to napraviti. Za učinkovito korištenje standarda potrebno je podrobno razumijevanje navedenih zahtjeva i njihovu primjenu na način koji odgovara tvrtki i njezinom poslovnom okruženju.
Norma ISO 55002 daje smjernice za implementaciju standarda ISO 55001 u poslovanje tvrtke. Razrađuje i detaljno pojašnjava zahtjeve navedene u ISO 55001 te daje primjere koji će pomoći u razumijevanju tih zahtjeva.
ISO 550012 nije vodič za autostopere, kontrolna lista niti skup pravila koje mogu sve tvrtke primijeniti na isti način i očekivati iste rezultate već razrađen standard za uspostavu cjelovitog sustava u svrhu unaprijeđenja poslovanja.
Sada kad smo razjasnili temeljni sadržaj svakog standarda, krenimo na konkretna pitanja.
1. Što je “imovina”?
Standard ISO 55000 definira imovinu kao „fizičku stvar, entitet koji ima potencijalnu ili stvarnu vrijednost za svojeg vlasnika“. Imovina može biti fizička ili intelektualna poput komada opreme, stroja, zgrade, postrojenja, brenda, reputacija kompanije i sl.
2. Čemu služe standardi ISO 55000, ISO 55001 i ISO 55002?
Njihova svrha je omogućiti iskorištavanje imovine na najbolji mogući način koji će donijeti korist tvrtki i svima uključenima.
Sustav upravljanja imovinom pruža cjelovit pristup koji će smanjiti troškove vlasnicima tijekom čitavog životnog ciklusa opreme, smanjiti rizik od obustave proizvodnje, kvarova i drugih poteškoća u poslovanju koji dovode do gubitaka.
Norme primjenjuju princip od vrha prema dnu u kojem donošenje odluka kreće od najvišeg menadžmenta i prenosi se duž čitave kompanije integrirajući upravljanje imovinom u strategiju kompanije.
3. Kome su potrebne norme ISO 55000, ISO 55001 i ISO 55002?
Norme su potrebne tvrtkama i organizacijama u industrijskim sektorima transporta, građevine, telekomunikacija, upravljanja nekretninama, u energetskom sektoru, rudarstvu, proizvodnji, inženjerskim djelatnostima, javnoj upravi i sektoru upravljanja prirodnim resursima.
4. Koja je razlika između normi ISO 90001 i ISO 55001?
Norma ISO 9001 određuje kriterije za upravljanje sustavom osiguranja kvalitete u tvrtkama ili organizacijama po metodologiji planiraj-izvrši-kontroliraj-djeluj (PDCA plan-do-check-act) i koristi procesno orijentiran pristup dokumentaciji uz reviziju strukture cjelokupnog sustava rada, odgovornosti, procedura i metoda osiguranja kvalitete.
ISO 55001 se fokusira isključivo na upravljanje fizičkom imovinom tvrtke.
5. Koje tvrtke i organizacije koriste normu ISO 55001?
ISO 55001 se može primijeniti u bilo kojoj organizacija koja posjeduje i upravlja fizičkom imovinom poput aviokompanija, brodara, željeznica, elektrana (nuklearnih, termo, hidro, na obnovljive izvore), petrokemije, rudarstva, naftne industrije, proizvodnje, sustava prijenosa i distribucije električne energije, telekomunikacija i sl.
6. Koje novosti uvodi ISO 55001 u sustav upravljanja imovinom?
Sustav upravljanja strojevima i opremom opisan u ISO 55001 neće zamijeniti dosadašnje dobre prakse, strategije, politike, programe i alate u upravljanju održavanjem opreme. Osmišljen je da bi pružio povezani okvir unutar kojega svi elementi mogu učinkovito funkcionirati.
Po prvi put dobili smo cjeloviti sustav upravljanja održavanjem opreme.
Nemojmo se zavaravati, ISO 55001 nije čarobni lijek koji će otkloniti sve nedostatke dugogodišnjeg nedostatka održavanja, probleme nastale uslijed nekvalitetne konstrukcije ili kvarove nastale zbog procesnih uvjeta.
Međutim, ISO 55001 omogućava tvrtki alate za osiguravanje dosljednog upravljanja održavanjem imovine, potrebne resurse i koordinaciju među svim sudionicima.
7. Što je cjeloviti životni ciklus imovine?
Posao odrađen u fazi konstrukcije kapitalnih projekata kasnije ima utjecaj na troškove održavanja cjelokupne imovine (strojeva i opreme).
Imamo brojne primjere gdje je tvrtka mogla biti pošteđena skupog i kompliciranog održavanja opreme da su bolje odluke bile donesene u ranijim fazama projekta.
Nedovoljno planiranje i kontrola u fazi konstruiranja doveli su do kroničnih problema s pouzdanosti i često zahtijevati skupe prilagodbe kako bi čitav sustav mogao funkcionirati tijekom životnog ciklusa određenog stroja ili komada opreme.
Međutim, brojne tvrtke i dalje provode rascjepkan pristup upravljanja imovinom gdje svaki odjel ima drugačije ciljeve i pokazatelje uspješnosti.
Zbog navedenih razloga, ISO 55001 omogućava model sustava upravljanja imovinom koji temeljem dobre prakse i poštujući zakonske okvire razmatra čitav životni ciklus imovine od faze projektnog rješenja sve do faze rashoda, što je prikazano na slici 1.
U svakoj fazi se pažljivo razmatraju svi elementi kako bi se u konačnici smanjio ukupni trošak održavanja imovine.
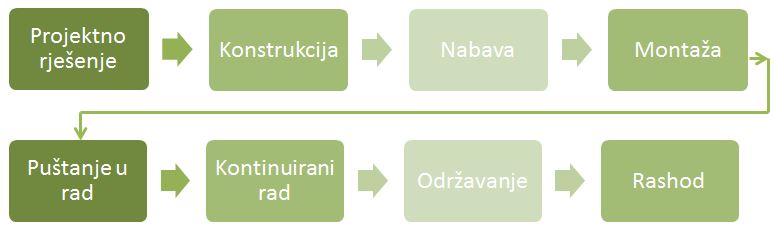
Slika 1. Životni ciklus imovine
8. Je li ISO 55001 zanimljiv za menadžment?
Svakako da jest, zato što će donijeti dobrobit čitavoj tvrtki. Menadžment brojnih tvrtki je postao svjestan da njihovi konkurenti primjenjuju ISO 55001 dok su budući potencijalni klijenti postali svjesni da je posjedovanje certifikata ISO 55001 u današnje vrijeme stalna stavka svakog poslovnog ugovora.
Ako vaš menadžment do sada nije razmatrao pripremanje tvrtke za uvođenje certifikacije ISO 55001, krajnje je vrijeme da započne.
Jedan od načina na koji se menadžmentu može ukazati na prednosti uvođenja ISO 55001 je provođenje istraživanja sustava upravljanja imovinom koje će ukazati na nedostatke postojećeg stanja u odnosu na ISO 55001.
Istraživanje treba rezultirati izvještajem koji će navesti sve prilike za poboljšanja i potencijalne uštede.
9. Kako pokazati kolegama prednosti ISO 55001?
Ako ste prošli obuku za ISO 55001, mogli biste organizirati neformalnu radionicu i upoznati kolege s prednostima. Ako menadžment odobri inicijativu za razvoj sustava upravljanja imovinom, komunikacija unutar kompanije treba uključivati sve zaposlenike i poduprijeti uvođenje ISO 55001.
U tom slučaju će vaši kolege dobiti detaljniji pregled što predstavlja ovaj certifikat i koje zahtjeve treba ispuniti kako bi se iskoristile sve prednosti.
10. Koje korake treba poduzeti moja tvrtka ako se odluči za certifikaciju?
Ne postoji jedinstvena formula ili jednoznačni vodič za certifikaciju. Svaka tvrtka je drugačija s obzirom na veličinu, vrstu proizvoda, broj zaposlenika, organizacijsku kulturu, sustave kontrole i proizvodne procese.
Npr. ISO 55001 certifikacija za tvornicu koja proizvodi lijekove će se razlikovati od certifikacije tvornice koja proizvodi alkoholna pića.
Kako bi sustav upravljanja imovinom bio učinkovit i donio dugotrajnu korist, mora biti prilagođen isključivo promatranoj tvrtki. To se postiže primjenom odgovarajuće strategije i akcijskog plana koji definira korake potrebne za usvajanje strategije.
Prvi korak je razgovor s konzultantom specijaliziranim za ovu vrstu certifikacije ili s certifikacijskom kućom o zahtjevima koje treba ispuniti.
Potom, treba napraviti analizu tvrtke da se odrede nedostaci i prostor za usklađivanje. Rezultati analize moraju pokazati strategiju za postizanje usklađenosti prema zahtjevima certifikacije i troškove implementacije strategije.
Pritom treba što više naučiti od konzultanta i usvojiti korisne vještine koje će vam trebati na nastavak rada na certificiranim procedurama jednom kada konzultant ode.
11. Je li dobro usvojiti principe norme ISO 55001, ali ne proći postupak ovlaštene certifikacije?
Pod određenim uvjetima jest. Realno, ISO 55001 certifikacija nije za svaku tvrtku i ne treba pošto poto uletjeti bez razumijevanja prednosti koje bi ovakva certifikacija donijela za poboljšanje postojećeg poslovanja ili povećanje budućih profita.
Primjena normi navedenih u ISO 55001 i sam postupak certifikacije su 2 različite stvari.
Pametnom primjenom ISO 55001 norme, tvrtka može postići odličan sustav upravljanja imovinom. Rezultat će biti sustav koji omogućava tvrtki upravljanje imovinom ili imovinskim portfeljem na učinkovit, produktivan i profitabilan način.
Prednosti opravdavaju trošak razvoja i primjene sustava upravljanja imovinom.
Vaša tvrtka može uz pomoć zaposlenika razviti i implementirati sustav upravljanja imovinom bez plaćanja konzultanata te izbjeći trošak skupog certificiranja od strane ovlaštene kuće.
Drugo je pitanje hoće li tvrtka moći podići poslovanje na višu razinu i sklapati profitabilnije poslove bez dokaza o certifikaciji.
12. Je li standard ISO 55001 u suprotnosti s ISO 9001, ISO 14001 i drugim ISO standardima?
Nije u suprotnosti, na kraju krajeva, razvila ga je ista međunarodna organizacija za standardizaciju. Bilo kakva suprotnost može proizaći jedino iz strukture upravljačkog sustava ili same politike upravljanja kompanijom, pa je potrebno istražiti situaciju u pripremnoj fazi prije početka implementacije ISO 55001.
Ako se pojave problematična pitanja, treba direktno konzultirati https://www.iso.org/contact-iso.html s konkretnim pitanjem ili provjeriti s konzultantom ili ovlaštenom kućom.
13. Već smo stekli certifikat ISO 9001. hoće li nam osigurati prednost pri stjecanju ISO 55001 certifikata?
Vrlo vjerojatno hoće. Sustav upravljanja kvalitetom obuhvaćen certifikatom ISO 9001 bi trebao ispunjavati brojne zahtjeve ISO 55001.
Oba standarda imaju dovoljan broj zajedničkih zahtjeva.
14. Koliko treba vremena za uspostaviti sustav upravljanja imovinom?
Na ovo pitanje nema jednoznačnog i konkretnog odgovora koji bi odgovarao za sve tvrtke.
Vrijeme potrebno za razvijanje sustava upravljanja i implementaciju sa zadovoljavajućim rezultatima ovisi o veličini tvrtke, njenim poslovnim procesima i brojnim drugim specifičnostima (sjetite se prethodnog primjera tvornice lijekova i alkoholnih pića).
Na vrijeme trajanja utječe i pritisak s razina višeg menadžmenta ako je ISO 55001 standardizacija u kompanijskim ciljevima za tekuću godinu.
Nekakav vremenski prosjek iznosi 3 do 6 mjeseci za usvajanje sustava upravljanja imovinom nakon čega dolazi ovlaštena kuća za certificiranje. Vremenski period mora biti dovoljno dug da omogući prikupljanje dokumentacije o provedenim procedurama koje će biti dane kao dokaz na uvid certifikacijskoj kući u svrhu potvrđivanja sukladnosti.
Vremenski period se obično utvrđuje prilikom analize nedostataka u postojećem sustavu upravljanja imovinom.
15. Je li ISO 55001 moguće uskladiti s postojećim sustavom upravljanja tvrtkom?
U slučaju brojnih tvrtki odgovor je potvrdan. Norma ISO 55001 specificira koje zahtjeve treba ispuniti sustav upravljanja, međutim nigdje ne brani integraciju u postojeći sustav upravljanja tvrtkom.
Neki zahtjevi se obavezno moraju integrirati kao to su pristup upravljanja imovinom temeljem životnog ciklusa, povezanost strategije upravljanja imovinom i strategije tvrtke, suradnja među različitim sudionicima i sl.
Međutim, mogu se javiti situacije gdje je u teoriji uskalđivanje sjajno rješenje ali u praksi uopće ne funkcionira.
16. Tko sve mora biti uključen u provedbu normi?
Svi pretpostavljaju da djelatnici tehničkih struka moraju biti uključeni, no što je s ostalim djelatnicima? Sustav upravljanja imovinom je zajednički posao i tiče se svih.
Uključuje konstruiranje i razvoj, ugovaranje, nabavu, održavanje, kontroling i financije, marketing, odnose s javnošću, ljudske potencijale, zaštitu okoliša, zdravlja i sigurnosti, pravne poslove te sve druge koji čine tvrtku.
Važno je da se svi zajednički uključe prilikom razvijanja sustava upravljanja imovinom.
Jeste li krenuli s usvajanjem principa ISO 55001 i 55002 standarda? Kakva su vaša iskustva s uvođenjem sustava upravljanja imovinom? Podijelite ih u komentarima! Pitanja, komentare i mišljenja također možete uputiti na mail katarina_knafelj@hotmail.com