U prethodnom članku upoznali smo se s elementima pravilnog podmazivanja i osnovama konstrukcije aksijalnih odrivnih ležajeva sa samopodesivih segmenata, koji uz pravilno održavanje mogu imati dugi životni vijek. Međutim, svi su elementi strojeva podložni trošenju i habanju kada se poremete njihovi radni uvjeti tijekom duljeg vremenskog perioda. Danas ćemo vidjeti koja su najčešća oštećenja odrivnih ležajeva, znakove po kojima ćemo ih prepoznati te koje korektivne radnje primjeniti kako bismo spriječili da dođe do oštećenja ili sanirali oštećenja nakon što se dogode.
Neka od opisanih oštećenja se javljaju pojedinačno, a ponekad dolazi do kombinacije dvaju ili više tipova oštećenja zbog sličnih uzroka, npr. trošenja, dubokih ogrebotina i abrazije, gubitka uljnog filma uz djelovanje preopterećenja i sl. Brzina vrtnje na obodu odrivnog ležaja se kreće od 30 m/s do 100 m/s pri čemu tlak na površini ležaja iznosi 0,1 bar do 30 bar i ove radne uvjete treba uzeti u obzir pri analizi nastalih oštećenja.
Krenimo redom:
1. Trošenje metala se odražava na površinama koje su bile u međusobnom kontaktu, mijenja se boja na površini i nastaju udubljenja. Trošenje je posljedica povećanih (prevelikih vibracija) kroz dulje vrijeme, djelovanja prevelikog opterećenja na segmente te smanjenja kontaktne površine koja nosi opterećenje. Nastala oštećenja se otklanjaju prelijevanjem odrivnih segmenata novim slojem bijelog metala i strojnom obradom na potrebnu debljinu, ustanoviti gdje dolazi do preopterećenja i zašto te nastojati smanjiti preopterećenje te ponovno centrirati stroj i otkloniti uzrok povećanih vibracija.
2. Erozija se prepoznaje po nastalim urezima na površini bijelog metala koji se protežu u smjeru rotacije ležaja ili po tragovima trošenja. Eroziju uzrokuje djelovanje čestica metala ili prljavštine koje se zateknu u uljnom filmu i stružu po površini bijelog metala te velika brzina strujanja fluida čime se drastično smanji debljina uljnog filma i posljedično, nosivost opterećenja.
Eroziju možemo spriječiti filtriranjem i ispiranjem sustava podmazivanja prije nego se stroj pokrene u rad, redovitom zamjenom mrežice/uloška filtera te saniranjem odrivnih segmentata na način da se preliju bijelim metalom i potom strojno obrade na potrebnu debljinu.
3. Duboke ogrebotine ili risevi na površini nastaju u vrlo kratkom vremenu kao posljedica struganja krupnijih metalnih čestica ili prljavštine po bijelom metalu. Vratila izrađena od legura koje u svom sastavu sadrže krom ili mangan u udjelu od 2% do 14% nisu kompatibilni sa bijelim metalom, dok će uljna emulzija zbog prisustva vode dovesti do nastanak tankog sloja oksida na površini. Provjerite od kojeg su materijala načinjeni vratilo, odrivni prsten i odrivni segmenti, danas je to moguće primjenom PMI metode ili laboratorijskom analizom strugotine materijala. Ako analiza pokaže nekompatibilnost, zamijenite vratilo ili odrivni ležaj sa drugima izrađenim od odgovarajućih materijala.
4. Abrazija se javlja u obliku paralelnih ogrebotina uz obod odrivnog segmenta koje se pogoršavaju tijekom vremena. Uzrokuju je čestice metala ili prljavštine koje imaju veći promjer nego što je debljina uljnog filma. Kroz nastale ogrebotine ulje „bježi“ pa se smanjuje debljina uljnog filma. Obavezno redovito kontrolirajte čistoću ulja, redovito mijenjajte uloške filtera te izmijenite cjelokupnu količinu ulja pri svakom servisu stroja uz ispiranje sustava podmazivanja.

Slika 1.: Oštećenja segmenata odrivnog ležaja 1. – 4.
5. Zamor materijala odrivnog ležaja uzrokuje preveliko dinamičko opterećenje, pregrijavanje tijekom rada, necentričnost, visoke vibracije ili pogrešna montaža. Prepoznaje se po sitnim uzdužnim pukotinama na površinama bijelog metala odrivnih segmenata na mjestu gdje je djelovalo opterećenje. Pukotine se ne šire u dubinu. Spriječavanje zamora materijala je zapravo spriječavanje djelovanja prevelikog dinamičkog opterećenja, pravilna montaža ležaja, izbor ležaja koji podnosi veće radno opterećenje te pravilno centriranje stroja.
6. Točkasta elektro korozija (pitting) se primjećuje u obliku velikog broja malih jednoliko raspoređenih rupica (udubljenja) koncentriranih na određenom dijelu površine bijelog metala odrivnog ležaja te na vratilu stroja, najčešće tamo gdje je uljni film bio pretanak da stvori izolaciju. Dolazi do pojave elektrostatičkog naboja između vratila i ležaja te stvaranja elektromagnetskih struja zbog vrtnje vratila. Potrebno je provjeriti uzemljenje stroja, kvalitetu ulja za podmazivanje i pregledati ležajno kućište za slučaj da se u njemu kondenzira vlaga te stvara emulziju koja narušava kvalitetu ulja smanjujući sposobnost uljnog filma da stvori dovoljno debeo sloj izolacije.
7. Mjehuri na površini bijelog metala su posljedica izdvajanja vodika iz kristalne rešetke i njihovo gomilanje na granicama kristalnih zrna, pri čemu dolazi do mehaničkog pucanja veze. Površina bijelog metala se mora prebrusiti, preliti novim slojem bijelog metala i strojno obraditi na potrebnu debljinu.Potrebno je provjeriti sastav materijala od kojeg je odrivni ležaj izrađen.
8. Necentričnost ležaja je uzrokovana koncentracijom radnog opterećenja na samo jednoj strani odrivnog ležaja, aksijalnim pomakom između centralne osi ležaja i vratila, necentrično ugrađenim kućištem ili necentrično postavljenim vratilom. Posljedice se primjećuju na odrivnim segmentima koji budu istrošeni samo s jedne strane, one na kojoj je radno opterećenje djelovalo većim intenzitetom, lokaliziranog trošenja bijelog metala, povećane temperature ležaja i zamora materijala na dijagonalno suprotnim strana od onih na kojima je djelovalo povećano opterećenje.
Necentričnost spriječavamo tako da demontiramo ležaj i ponovno ga montiramo pazeći i provjeravajući više puta centriranost pomoću komparatora. Ako se problem i dalje ponavlja, potrebno je razmotriti ugradnju drugačijeg tipa ležaja koji će biti otporniji na pojavu necentričnosti, npr. samopodešavajući klizni ležaj.
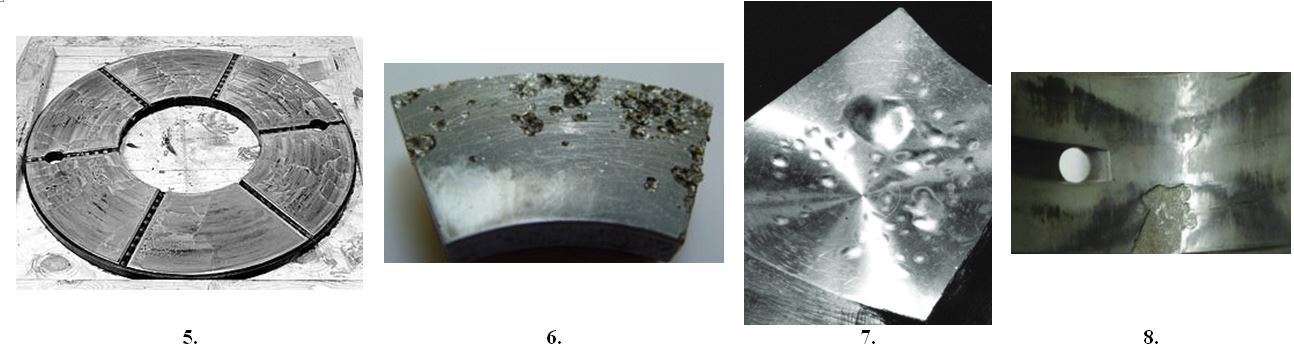
Slika 2.: Oštećenja segmenata odrivnog ležaja 5. – 8.
9. Pregrijavanje se primjećuje po naslagama smeđe boje nalik na lak na površinama gdje je djelovala visoka temperatura, promjenama boje čelika i lokaliziranih sitnih pukotina. Uzroci pregrijavanja odrivnog ležaja su prevelika brina vrtnje ili preveliko radno opterećenje, nestanak uljnog filma, previsoka temperatura ulja, nedovoljna zračnost i nedostatak hlađenja. Pregrijavanje ćemo spriječiti redovitim čišćenjem hladnjaka ulja, povećanjem protoka ulja te povećanjem nosivosti ležaja.
10. Cikličko grijanje/hlađenje ostavlja na površinama odrivnih segmenata reljefni uzorak, pri čemu dolazi do pukotina na granicama metalnih zrna. Uzroci su ponavljajuća izloženost naglim promjenama temperature koja uzrokuju ekspanziju kristalnih rešetki u bijelom metalu ili povećana koncentracija kositra u bijelom metalu, s obzirom da kositar nema dobru termičku stabilnost. Preporučuje se izbjeći izlaganje odrivnog ležaja naglim promjenama temperature tijekom rada te preliti segmente novim slojem bijelog metala poznatog kemijskog sastava (ovo rješenje je relativno brzo, cjenovno pristupačno u usporedbi sa kupovinom novih segmenata i kao što ćete primjetiti kroz ovaj članak, pomaže u brojnim situacijama).

Slika 3.: Oštećenja segmenata odrivnog ležaja 9. – 12.
11. Djelovanje preopterećenja je vidljivo po dubokim risevima na površni ležaja, udubljenjima i kružnim tragovima na obodu odrivnih segmenata. Preopterećenje je posljedica rada pri uvjetima izvan konstrukcijski dozvoljenih, nedostatka odgovarajuće debljine uljnog filma, previsoke temperature ulja, neodgovarajuće viskoznosti ulja ili pogrešne zračnosti. Preopterećenje odrivnog ležaja ćemo spriječiti tako da provjerimo postojeću nosivost i radne uvjete, ugradimo ležaj koji je konstrukcijski odgovarajući da može podnijeti radno opterećenje ili povećamo kapacitet nošenja radnog opterećenja.
12. Gubitak uljnog filma uzrokuje nedovoljna količina ulja za podmazivanje ili ulje neodgovarajućeg viskoziteta, distorzija odrivnih segmenata ili naglo povećanje radnog opterećenja prilikom pokretanja stroja. Posljedice gubitka uljnog filma se vide u obliku polirane površine ležaja, posebno bijelog metala te nedostatka pukotina. Osnovni način spriječavanja oštećenja je osigurati dovoljnu količinu ulja za podmazivanje odgovarajućeg viskoziteta te prije montaže provjeriti geometriju odrivnih segmenata jesu li površine ravne i pravokutne.
Koja oštećenja odrivnih ležajeva ste susretali? Koji su bili uzroci oštećenja? Podijelite iskustva u komentarima!